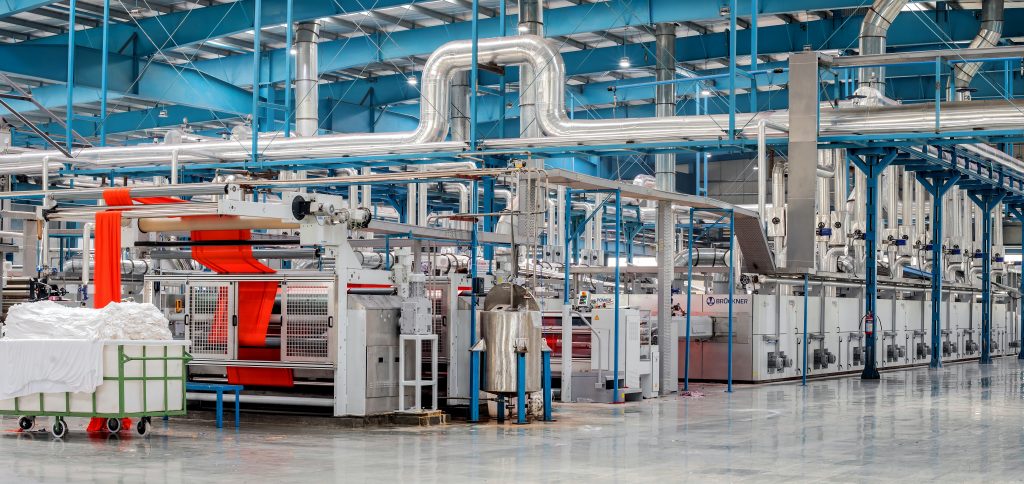
Photo by Lalit Kumar on Unsplash
Safety laws surrounding manufacturing are strict, both in the UK, the US and worldwide. Keeping up with compliance is essential to avoid lawsuits but keeping staff safe is an ethical obligation for manufacturing firms, and breaches could damage reputations. Fortunately, the guidelines for safety are clear-cut, which means we’re able to discuss the four essentials below.
Housekeeping
The nature of manufacturing means that work areas get messy which, when left unchecked, can lead to horrific accidents. Keeping workspaces clear of slips, trips, and unnecessary clutter is essential and should be worked into a robust cleaning schedule. As well as set clearing tasks, businesses should nurture a “clean as you go” culture, which should lead to less mess in the first instance. If an area of the warehouse becomes covered in oil or needs a deep cleaning, put hazard tape up to prevent traffic.
Risk Assessments
Risk assessments should be carried out before a business opens its doors but needs to be updated regularly. A thorough risk assessment gives you the opportunity to seek hazards and come up with actions to mitigate the risk. If you’re visited by a health inspector, you can use your assessments as evidence of your due diligence. If you feel unsure about carrying out a compliant risk assessment, you can hire a professional to conduct one for you.
Through the course of your risk assessment, you will find solutions to hazards. For example, you may need to put appropriate industrial signage up, which you can purchase through TagTec. Their catalogue of signage is extensive and includes fire safety, scaffolding tags, and gas cylinder tags. Alternatively, if you need a bespoke tag, they can create that for you as well.
Install Proper Protection
Manufacturing managers need to ensure workplaces are set up with safety at their core. To do this, protective mechanisms need to be installed to keep injuries at bay. For example, sheet forming machines should have guards on them to keep fingers out of the chopper. Further, guardrails should be installed around the work area, to prevent unqualified and unnecessary people from entering. If you fail to have these essential safety features installed, you can end up with costly accident lawsuits on your hands.
Offer Ongoing Training
You can put all the safety features in place, but if your staff don’t know how to use it, they’re pretty useless. Therefore, you need to make sure your staff are trained before they use any equipment. Then, throughout their life in the business, ongoing training should be given to consolidate learning and update their knowledge base. When carrying out training, make sure everything is documented and signed, which will eliminate claims of improper training leading to injury.
Within the manufacturing industry, workers carry out a multitude of dangerous tasks, which is why their safety needs to be a top priority. A great place to start the process is with a thorough risk assessment, which will give you the opportunity to think about how you will mitigate risks.