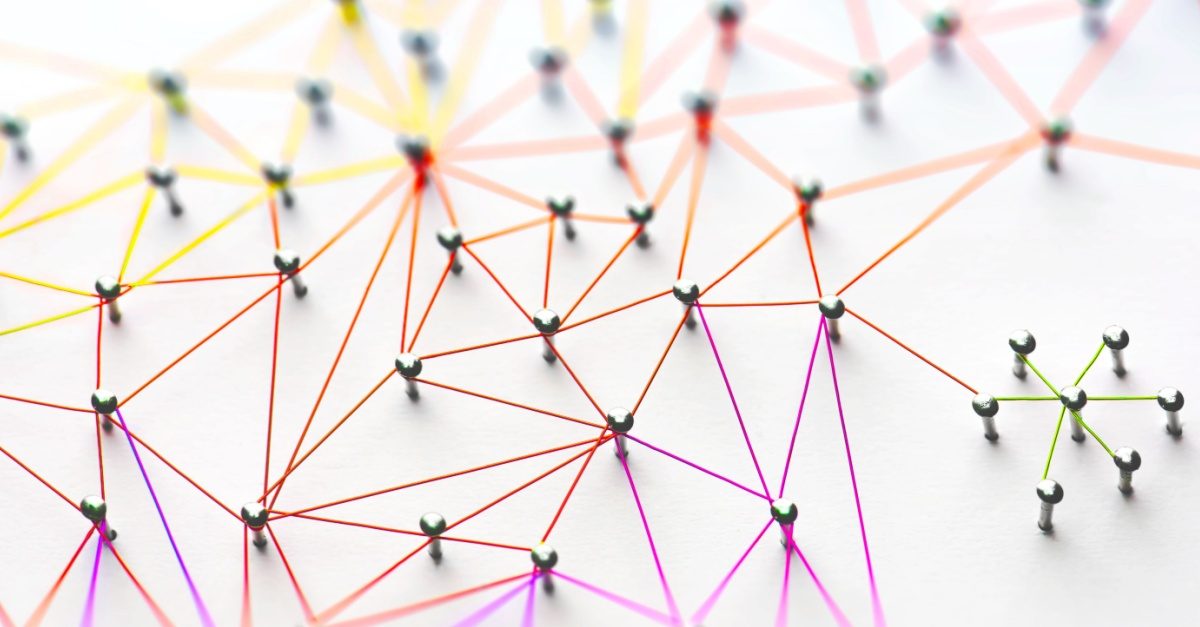
Your Guide to Mastering Multi-Party Supply Chain Communications
Navigating changing customer landscapes, natural disasters, and supply chain disruptions means mastering instant updates and responsive actions.
The harsh reality is that many businesses, trucking or otherwise, are still grappling with the challenges of adapting swiftly to slowdowns and bottlenecks, often paying a hefty price in lost opportunities and revenue. For example, the number of authorised US trucking fleets dropped by nearly 9,000 in the first quarter of 2023. What’s more, the current solutions designed to enhance communication in the supply chain process come with their own fair share of limitations and unexpected pitfalls. Read our guide to Mastering Multi-Party Supply Chain Communications.
Consider email–a communication tool that, despite its widespread use, lacks the robust security features necessary for safeguarding sensitive information. The unstructured nature of emails makes retrieving crucial data during disputes akin to searching for a needle in a haystack. Lost emails, incomplete attachments, and multiple threads on the same topic only compound the chaos.
In the face of evolving complexities, where multiple solutions, vendors, functional service centres, and applications intersect, businesses must reckon with the potential fallout of even the smallest communication glitch. Losing an email that documents a crucial change in an order’s information or highlights compatibility issues between buyer and supplier systems can send shockwaves throughout the organisation.
Prioritising communication is the key to an efficient supply chain.
Prevalent Challenges in Multi-Party Supply Chain Communication
When everyone has their own secret stash of details and refuses to or simply doesn’t share, they can hamstring an entire multi-party supply chain. Specific issues of this nature can include classic communication gaps and delays, lack of harmony in technology and platform consistency, and more.
Information silos and lack of transparency
Information silos wreak havoc on productivity, collaboration, and innovation. When different departments or teams do their own thing, they often fail to collaborate and communicate. They become so engrossed in their own projects and goals that they forget there’s a whole archipelago of potential collaboration. The result? Duplication of effort–two teams unknowingly working on the same thing–and missed opportunities for innovation.
Then there’s the impact on important aspects like productivity or even compliance.
Before committing to any new supply chain partner, you should assess all potential risks of that partnership. Legal compliance is just one aspect to avoid potential disruptions. Let’s look at an example involving compliance with legal and regulatory standards.
If you’re committing to a new logistics and transportation provider, you should ask them to walk you through their process step by step. Checking things like their fleet insurance coverage is crucial to minimise your risks down the line. The authorities often mandate insurance coverage, and not complying with this requirement might result in suspended operations. Naturally, this is a disruption for the whole supply chain.
Insurance coverage is just one of the many things that should be checked and aligned. Before committing to any party, dive deep into the risk assessment. If the partner is transparent, it’s a good sign that you can trust them, and the collaboration will succeed.
Communication gaps and delays
Poor communication in the supply chain isn’t just a minor hiccup; it’s a major roadblock that can bring the entire operation to a halt. Imagine a highway with no traffic signals or road signs–chaos, right? What happens if information isn’t easily available to all stakeholders throughout the supply chain?
When issues can’t be raised quickly and efficiently, you’re looking at a recipe for disaster. Products and materials start piling up, leading to wastage and backlogs resembling logistical traffic jams. It’s not just about goods sitting idly; it’s about unmet demand. And in the supply chain world, unmet demand translates to lost opportunities and revenue. Did you know that businesses that embrace newer, more integrated communication systems see a 20% increase in efficiency? Communication is the key to better problem-solving.
Technology and platform inconsistencies
Navigating the tech landscape in the supply chain is like walking through a maze, and the wrong turns can lead to severe inefficiencies. One major stumbling block is the tendency of some supply chain managers to avoid new systems altogether. Sure, old ways might seem comfortable, but resisting change can be costly in the ever-evolving world of technology.
As the Internet of Things (IoT) improves, the convenience and necessity of adopting new communication systems will only grow. The rate of change isn’t going to slow down, but emerging trends present opportunities to reduce costs, shrink carbon footprints, and elevate customer service.
There are also inefficiencies in using the wrong applications–a classic case of the grass looking greener on the other side. The pressure to stay competitive and innovative can prematurely lead supply chain managers to jump on the smart technology bandwagon. However, implementing new systems without clearly understanding how they consolidate and improve operations can create unnecessary complications.
Resulting misalignment in goals and deliverables
Ensuring supply chain alignment and fostering collaboration creates a well-oiled and efficient operation. Let’s break down some key tips to make sure your supply chain is not just moving but moving in sync:
- Define Common Goals and Metrics
Clearly define common goals and metrics that resonate through the supply chain. Whether it’s reducing lead times, minimising costs, or improving customer satisfaction, having a shared vision ensures everyone plays for the same team.
- Communicate Effectively and Frequently
Communication is the heartbeat of collaboration. Regular and open communication channels are vital. Keep the information flowing–from updates on inventory levels to potential disruptions. This helps proactively address challenges and ensures that everyone involved is well-informed and prepared.
- Leverage Technology and Data
Implementing advanced systems, like real-time tracking, IoT, and data analytics, provides visibility into the entire supply chain. This helps identify bottlenecks and enables quick decision-making based on accurate, up-to-date information.
- Foster a Collaborative Culture and Mindset
Encourage a culture where collaboration is not just a buzzword but a daily practice. This means breaking down silos between different departments and fostering a spirit of teamwork.
The Most Effective Communication Strategies for an Effective Multi-Party Supply Chain
So, how do you become a supply chain master? We recommend implementing the following strategies to help improve your overall communications:
Promoting data transparency and sharing
Accurate supply chain data is the glue that holds product availability together and safeguards a brand’s image. It’s not just about numbers. Proper data handling requires reputation, growth, and staying ahead in the race.
A Nielsen IQ report revealed that 80% of the crowd agrees–sharing data is no longer a choice; it’s a lifeline. Data sharing, in its essence, involves making the necessary information available to the right players within the ecosystem.
Data sharing fosters better collaboration and communication within the ecosystem. When organisations seamlessly share data, they unlock a treasure trove of opportunities, such as:
- Improved efficiency
- Sharper decision-making skills
- An edge that sets you apart in the marketplace
Real-time visibility into inventory and order status
Real-time inventory and order status visibility provide a clear view of the logistics landscape, from suppliers and manufacturers to warehouses and end customers. Imagine driving without a GPS–you might get there, but it won’t be the most efficient route. Real-time visibility ensures businesses are on the right track, quite literally.
Insights into order whereabouts, inventory status, and logistics issues allow informed decision-making. Businesses can correct discrepancies on the fly, optimise routes, and eliminate unnecessary diversions, leading to cost savings and a high return on investment. It’s not just about reaching the destination; it’s about doing it in the most cost-effective way possible.
Customers expect their delivery experiences to resemble nothing less than royal treatment, with real-time transportation visibility being the crown jewel. Providing customers with live updates on delivery progress, ensuring transparency and reliability, actually empowers businesses in the long run. Quick adjustments based on last-minute changes in customer preferences make the delivery process smooth and delightful. It’s the key to winning hearts and loyalty in a competitive marketplace where fast and flawless deliveries are the norm.
Assigning clear responsibilities
Every team member should know their role and how it contributes to the grand tapestry of the supply chain. From the supplier providing raw materials to the end customer eagerly awaiting the product, we must make it crystal clear who does what. No room for confusion, no guessing games–just a smoothly synchronised team where accountability is the star of the show.
Leave no room for guessing in your supply chain. Outline the process, clearly marking what happens, who’s involved, and how it seamlessly connects to the next step. The customer is at the heart of the supply chain kingdom, so shine a spotlight on how each step in the process affects them. Whether it’s the timely delivery of a product or the quality of service provided, ensure that your team recognises how much of an impact their role has on delivering products and customer satisfaction.
Open training and education for stakeholders
Organising internal training among stakeholders is like fine-tuning an orchestra–everyone must be on the same page to create harmony. Conducting in-house training sessions brings your team together for a collective learning experience. Identify the specific areas where knowledge needs a boost and tailor the training to address the unique challenges and goals of your supply chain.
Sometimes, bringing in external professionals can add expertise to your training initiatives. Organisations like the Institute of Supply Chain Management (IOSCM) offer specialised courses and certifications designed to elevate supply chain management skills.
Establishing a feedback loop
Finally, creating a feedback loop in your supply chain is like installing a high-tech GPS–it tells you where you’ve been and guides you on the best route forward. Establishing a robust feedback loop can transform your supply chain into a well-tuned engine of efficiency, cost-effectiveness, and customer satisfaction.
In your supply chain, stakeholders wear many hats–employees, customers, suppliers–each with a unique perspective. We cast a wide net to gather feedback from all corners. What’s working? What needs improvement? By tapping into the collective wisdom of everyone involved, you get a 360-degree view of your supply chain landscape.
By analysing the input from stakeholders, you can identify areas for improvement. There could be a bottleneck in the process, a hiccup in communication, or an opportunity to streamline operations. It’s not just about finding problems; it’s about uncovering the potential for enhancement and growth to truly master your supply chain communications. #

Guarantee success in your supply chain with IoSCM. Find out how our qualifications, resources, support and expertise can help you. Call 0800 1422 522 today.