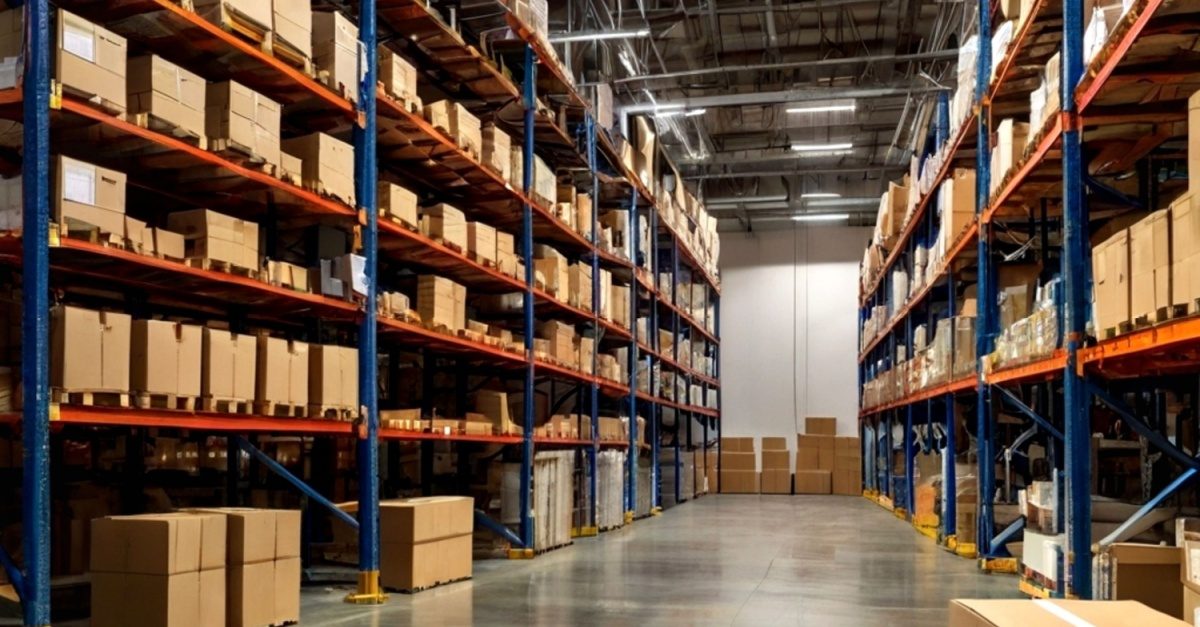
Workplace Safety in Warehouses: Best Practices for Leaders
In such a fast-moving sector, safety within the warehousing environment is essential. According to the latest data from the UK’s Health and Safety Executive (HSE), the transportation and storage sector experienced 26,000+ non-fatal workplace incidents in 2022/23. Slips, trips, and falls accounted for 31% of injuries, and 18% of injuries were sustained while lifting/handling. These associated statistics illustrate just a slice of the risk faced by workers on a daily basis, an essential responsibility and personal concern for managers and leaders.
Safety Starts at the Top
In a successful warehouse environment, it requires strong leadership to establish a safe workplace. When leaders and supervisors prioritise safety, it sets the tone for the culture. When employees witness their leader doing the right thing, they are much more likely to follow procedure.
One key to positioning yourself as a leader is to help foster a work environment where it is acceptable to openly communicate. Employees should feel comfortable reporting unsafe conditions, or near-misses, without any fear of retribution. Reporting incidents allows for early investigation of potential issues and establishes a common value or sense of responsibility for safety.
Know the Risks Before They Become Incidents
Once safety culture is in place, the next step is identifying the most common hazards. In most warehouses, these include:
- Slips, trips, and falls
- Collisions involving forklifts or other machinery
- Poor ergonomics leading to strain injuries
- Falling objects from shelves
Regular walk-throughs and formal risk assessments allow leaders to pinpoint these issues. Even simple actions—like better lighting or reworking a traffic route—can prevent injuries.
Use Technology to Support Safer Workflows
With risk areas identified, technology can step in to support safer operations. For instance, many warehouses now use automated alerts, sensors, and real-time inventory tracking to improve efficiency and reduce mistakes.
Another useful tool is video surveillance supported by cloud NVR. When positioned strategically, cameras can help monitor high-traffic or high-risk areas, providing extra visibility without disrupting workflow. This isn’t just about watching people—it’s about learning from patterns, analysing incidents, and supporting safety investigations.
Of course, it’s important to be transparent with staff about how these systems are used, ensuring compliance with local laws and protecting employee privacy.
Training Is a Safety Investment—Not a Task
Technology alone isn’t enough—employees need proper training to stay safe. Leaders should ensure safety training is ongoing, practical, and relevant. That includes:
- Safe lifting techniques
- Emergency procedures
- Operating machinery safely
- Using protective gear correctly
Make training hands-on and repeat it regularly. Refresher sessions, toolbox talks, and even quick morning safety huddles can help keep best practices top of mind.
Track Progress and Celebrate Wins
How do you know your safety efforts are working? Start by tracking key indicators:
- Number of incidents (and near misses)
- Safety training completion rates
- Equipment inspection logs
- Employee feedback and suggestions
When improvements are made, take time to recognise those responsible. A simple thank-you or shout-out at a team meeting can go a long way toward reinforcing positive behaviours.
FAQs
What’s the most common type of accident in warehouses?
The most common types of incidents that are reported in a warehouse environment are slips, trips, and falls. Many of these incidents can be avoided, and they are often due to preventable circumstances, such as wet flooring, uneven flooring, debris in the way, bad lighting, or loose products. Most slips, trips, and falls may seem minor, but they can be serious, resulting in fractures, sprains, and/or musculoskeletal injuries that can be long term.
With that in mind, to help eliminate or mitigate the risks of slips, trips, and falls the entire facility should focus on clear, dry pathways, use anti-slip mats when addressed, and follow proper housekeeping practices each day.
Are warehouse managers legally responsible for safety?
Yes, under UK Health and Safety law (Health and Safety at Work etc. Act 1974), as well as many international regulatory frameworks, warehouse managers and employers hold a legal duty of care. This includes assessing workplace risks, implementing safety controls, providing adequate training, and ensuring safe systems of work are in place. Failing to meet these responsibilities can lead to enforcement actions, fines, or even criminal prosecution in cases of negligence. Beyond the legal obligation, it’s also a vital part of ethical leadership and long-term operational success.
Can video surveillance be used for safety without invading privacy?
Absolutely. Video surveillance, when implemented transparently and ethically, can be a highly effective tool for improving safety. The key is to use cameras to monitor high-risk zones such as machinery areas, loading docks, or blind spots—rather than targeting individuals or using footage for disciplinary purposes. Under GDPR and data protection laws, employers must inform employees about camera use, explain the purpose, and store footage securely. When done correctly, video monitoring enhances situational awareness, supports investigations, and reinforces safe behaviour—without breaching employee trust or privacy rights.
How often should warehouse safety training be done?
Regular and consistent training is essential to maintain a safe warehouse. It is recommended that core safety training is refreshed every 6 to 12 months, depending on the nature of the operation and any changes in risk profile. Additional briefings or toolbox talks should be held whenever there are new hires, equipment, processes, or regulations introduced. Effective training isn’t just a one-off event—it should be part of a continuous learning culture, using a mix of hands-on instruction, visual demonstrations, and real-world scenarios to reinforce awareness.
What KPIs can help measure warehouse safety performance?
Monitoring the right Key Performance Indicators (KPIs) allows leadership to assess and improve warehouse safety over time. Some of the most effective KPIs include:
- Incident Rate: Number of reportable accidents or injuries per 100 employees.
- Near-Miss Reports: Frequency of reported near-misses—an indicator of proactive hazard identification.
- Training Compliance: Percentage of staff who are up-to-date with mandatory safety training.
- Equipment Maintenance Records: Timely checks and servicing of forklifts, conveyors, and other machinery.
- Safety Audit Scores: Results from internal or third-party audits measuring compliance and risk areas.
- Employee Safety Engagement: Participation rates in safety briefings, committees, or reporting systems.
Conclusion
Safety in warehouses is about more than just rules – it is about establishing a safety culture and empowering engaged, capable and safe people. Strong leadership is a factor in creating that culture. As this article describes, whether it is setting the tone from the top, implementing proactive safety initiatives, supporting and investing in training, or leveraging safety-improving technology like visual monitoring systems, effective safety leadership is both practical and strategic.
The FAQ’s above provide examples of the duty and layers of understanding about new products, projects or warehouse safety as a whole. From understanding your legal obligations and communicating them clearly, to how success can be measured with evidence-based KPI’s; a compassionate leader who oversees safety, listens and considers their teams emotional commitment to safety, and acts fairly will seriously reduce their risk of injury whilst improving productivity, staff morale and business continuity.
As time is the biggest cost in the warehousing industry, a proactive, well-managed, safety-conscious operation is without a doubt a competitive advantage.
At The Institute of Supply Chain Management (IoSCM), we offer a range of warehouse management and logistics courses which can help you to take the next step in your career. Our warehouse training programmes offer a modern approach to learning, taking into account your previous work experience and building your knowledge, so you can earn an industry-recognised qualification. We offer warehouse management courses ranging from level 2 to level 7, covering all aspects of the industry.