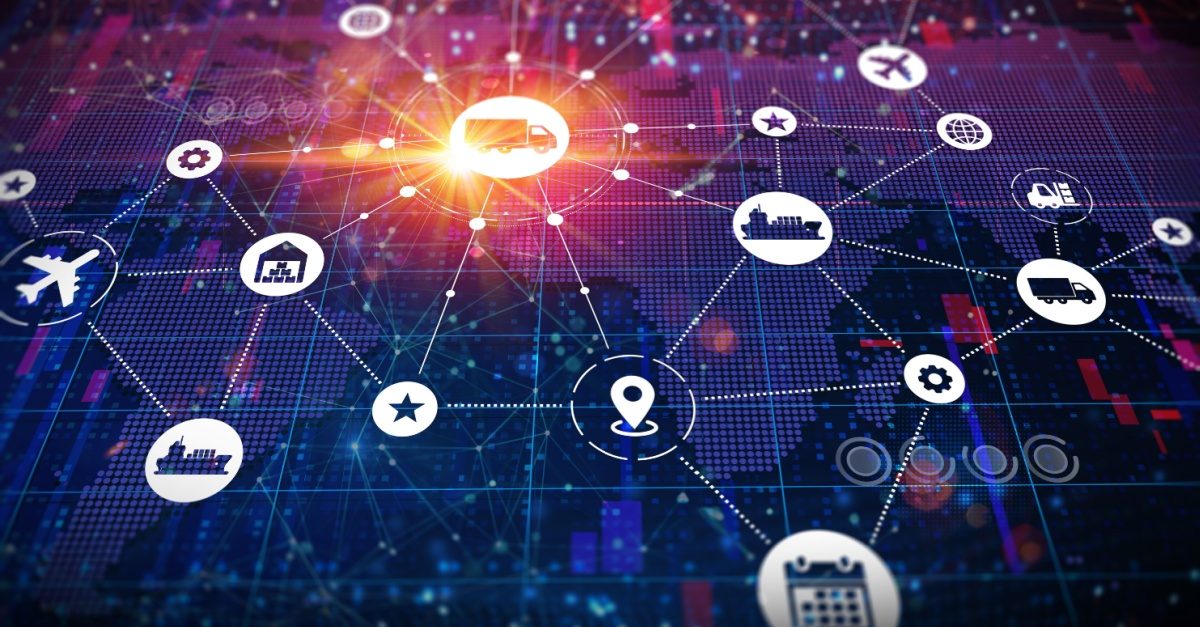
Understanding the Basics of Supply Chain Management
The products we use every day, from the clothes we wear to the phones we carry, all go through a journey before they reach our homes. That journey is managed and overseen through something we call supply chain management (SCM).
The concept is actually pretty simple, but very important. In today’s article, we’ll be exploring how supply chains work and why managing them effectively is crucial for the success of your business.
What Is Supply Chain Management?
Supply chain management (SCM) is the process of overseeing the flow of goods and services from the start to the end. It involves making the product from scratch, manufacturing, packaging, and delivering it to customers.
The main goal is to make sure products are made efficiently, delivered on time, and at the lowest cost possible. SCM also helps companies respond quickly to changes in demand, manage their inventory, and keep good relationships with suppliers and customers.
The supply chain is made up of different stages:
- Sourcing the materials: Gathering the materials needed for production.
- Manufacturing: Making the products.
- Packaging and warehousing: Getting the products ready to be sold and storing them.
- Distribution: Delivering the products to stores or to customers.
- Customer service: Handling returns, repairs, or any other issues that come up after a product is sold.
SCM is basically overseeing all of these steps and making sure they are as efficient as possible.
Why Does SCM Matter?
Supply chain management matters because it directly affects a business’s ability to make and sell products. If there’s a problem in the supply chain, it can lead to delays, higher costs, or poor-quality products, and all of this can affect a company’s reputation and lead to lost customers.
Here’s why SCM matters:
- Cost efficiency: By managing their resources well, companies can save money. For example, by choosing the best suppliers, avoiding overproduction, and optimising their transportation, businesses can reduce a lot of unnecessary costs and make sure they are using their money efficiently.
- Customer satisfaction: Quality supply chains mean products are always available when customers want them. A well-managed supply chain makes sure that products arrive on time and in good condition, which leads to happy customers and is great for business.
- Competitive advantage: Companies with strong SCM can respond faster to changes in demand, restock items more quickly, and offer lower prices, which gives them a huge competitive advantage.
- Risk management: SCM helps businesses prepare for risks. By having a plan, companies can handle unexpected situations better.
The Process of Supply Chain Management
Each part of this process plays an important role in making sure the supply chain runs competently. Here’s a look at how this process goes:
1. Planning
Before anything is created, companies need to make a plan. They need to figure out how much product is needed, when it’s needed, and where it should go. The goal of planning is to make sure that the right amount of product is produced.
Planning also involves managing inventory levels, forecasting demand, and creating a production schedule. Companies use software and data analytics to help predict how much of a product customers will want so that they don’t end up overstocking or understocking.
2. Sourcing
Sourcing is all about finding suppliers who can provide the materials or components a company needs to make its product. In this step, businesses negotiate prices, choose their suppliers, and do their best to make sure that the materials are delivered on time.
Building good relationships with suppliers is a key part of sourcing. A strong relationship makes sure that materials arrive as expected and that any possible issues can be resolved quickly. Sometimes, companies might even work with suppliers to improve processes or create more sustainable products.
3. Manufacturing
Once the materials are sourced, the next step is making the products. This involves the actual production process, quality control, and making sure the products are made according to the plan.
Efficiency is important at this stage. Companies focus on reducing waste, keeping costs low, and making sure the products meet quality standards. If something goes wrong during production, it can cause a lot of problems, since the most important thing in the process is the product itself.
4. Logistics
Logistics refers to how products are moved from one place to another. This could involve transporting materials to a factory or delivering the finished products to stores or customers.
Effective logistics means choosing the best transportation methods and making sure that products are delivered quickly. Logistics also covers warehousing (the place where products are stored before they are sold) and inventory management, which makes sure that there are enough products in stock to meet demand.
5. Returns Management
Not everything goes perfectly, and sometimes products need to be returned. Returns management is the process of handling these returns.
This part of SCM helps make sure that returns are handled efficiently and that customers have a good experience, even when something goes wrong. It also involves figuring out what to do with returned products.
The Key Principles of Effective SCM
Supply chain management (SCM) is all about making sure that goods flow smoothly from suppliers to customers. When done right, effective SCM can lead to happy customers, lower costs, and help businesses create a good reputation.
So, what are the key principles that make supply chain management effective? Here are a few you can try to implement:
1. Focusing on the Customer’s Needs
The most important thing in this whole process is the customer. It’s essential for businesses to understand what the customers want and do their best to give it to them. Companies should gather feedback and analyse customer behaviour to make sure that they can exceed their expectations.
By centering this process around the customers, businesses ensure they provide the right products at the right time and excellent service. This will result in customer satisfaction and loyalty. Remember, happy customers will always keep returning.
2. Collaboration
Collaboration is essential for a successful supply chain. This means building good relationships with everyone involved in the supply chain (suppliers, manufacturers, distributors, and retailers).
Open communication can help everyone involved reach their goals. You can connect with local suppliers and partners through platforms like Locanto to strengthen your supply chain network.
3. Flexibility
The business environment can always change, so it’s important for businesses to stay flexible. For example, if a popular product suddenly sees a spike in demand, a flexible supply chain can ramp up production quickly to meet that need.
Also, with all the technological advancements we have access to nowadays, in order for businesses to stay competitive, they need to find a way to integrate this knowledge. For example, inventory management systems help track stock levels in real time, and data analytics tools allow businesses to forecast demand accurately.
4. Constant Improvement
The world of supply chain management is always evolving, and there’s always room for improvement. Embracing a culture of constant improvement means regularly evaluating the processes, seeking feedback, and making the necessary adjustments.
Businesses can hold regular meetings to review performance, identify weak points, and brainstorm solutions.
Final Thoughts
Supply chain management might seem like a behind-the-scenes process, but it plays such an important role in making sure that the products we use every day are made and delivered efficiently.
An effective SCM requires careful coordination and good decision-making. And as technology continues to evolve, supply chains are becoming faster, more efficient, and more adaptable than ever before.
Bottomline: prioritising and improving your SCM will help keep customers happy. That is always good for business.