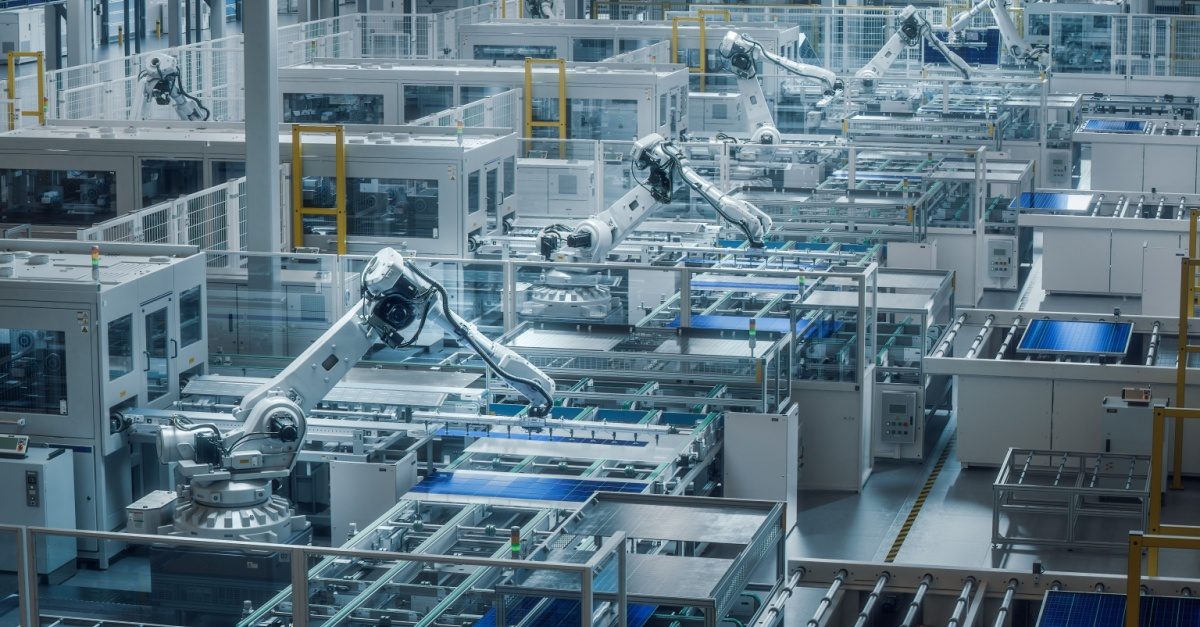
The High Cost Of Downtime In Manufacturing
In the competitive landscape of manufacturing, downtime emerges as a formidable adversary. When production lines unexpectedly falter, financial losses extend beyond mere productivity stalls. The true cost of downtime is a gradual erosion of a manufacturer’s most valuable asset: customer trust.
Operational Disruptions strain customer relationships.
Missed delivery deadlines due to operational disruptions strain customer relationships, pushing them towards alternative suppliers. Often, the root cause of these disruptions lies in overlooked maintenance, inadequate employee training, or deficient data management. These seemingly minor oversights can then escalate into catastrophic breakdowns. To counter these challenges, manufacturers must invest in preventative strategies.
Key Areas for Improvement
To mitigate downtime, manufacturers must identify key areas for improvement. By concentrating on these core areas, they can significantly enhance operational efficiency and overall business performance. These tactics are crucial for establishing a robust competitive advantage within the manufacturing industry.
Predictive Maintenance:
When leveraging data analytics and sensor technology, manufacturers can anticipate equipment failures and schedule maintenance proactively.
Employee Empowerment:
Comprehensive training programs empower employees to identify potential issues and take corrective actions.
Robust Supply Chain Management:
A resilient supply chain can mitigate disruptions caused by supplier failures or material shortages.
Inventory Optimisation:
Effective inventory management prevents stockouts and production delays.
Lean Manufacturing Principles:
Implementing lean methodologies can streamline processes, reduce waste, and improve overall efficiency.
Manufacturers can significantly reduce downtime, improve operational efficiency, and enhance overall business performance by focusing on these areas.
The Role of Technology
The integration of advanced technologies, such as the Industrial Internet of Things (IIoT) and artificial intelligence (AI), can revolutionise downtime management. Predictive maintenance platforms or equipment, powered by AI, can analyse equipment data to predict failures before they occur. For instance, when tracking torque values with a sensor torque, potential equipment issues can be detected early. Additionally, augmented reality (AR) can be used to guide technicians through complex repair processes, minimising downtime.
The Human Factor
While technology plays a crucial role in downtime prevention, the human element remains indispensable. A skilled and engaged workforce is essential for identifying potential issues, responding to emergencies, and implementing improvement initiatives. Investing in employee training, development, and well-being is crucial for building a high-performance manufacturing team. It is vital to foster a culture of continuous improvement and empowering employees to contribute to problem-solving.
Measuring the Impact of Downtime
To effectively address downtime, it is crucial to measure its impact on the business. Key performance indicators (KPIs) such as Overall Equipment Effectiveness (OEE) and Mean Time Between Failures (MTBF) can provide valuable insights into equipment performance and identify areas for improvement. By tracking these metrics, manufacturers can assess the effectiveness of their downtime reduction strategies and allocate resources accordingly.
Reducing downtime is paramount for manufacturing success.
When implementing proactive strategies, leveraging technology, and continuously monitoring performance, manufacturers can build a resilient operation that delivers consistent results and exceeds customer expectations. To explore practical solutions for minimising downtime within your manufacturing facility, refer to the accompanying resource. It offers actionable steps and highlights its crucial role in maintaining uninterrupted production processes.
Completing a manufacturing and production course with the Institute of Supply Chain Management (IoSCM) certifies your knowledge and skills to give you the best grounding for progression in your career. With our expert support network and unmatched resources, we provide more than just a manufacturing qualification – we give you the tools to grow, learn and progress as an industry professional.
Unlike other manufacturing and production training providers, we enable learners to develop their skills through a bespoke distance learning format, with support from industry experts every step of the way. You can custom-build your course to suit your current experience level, career ambitions, and employer objectives.