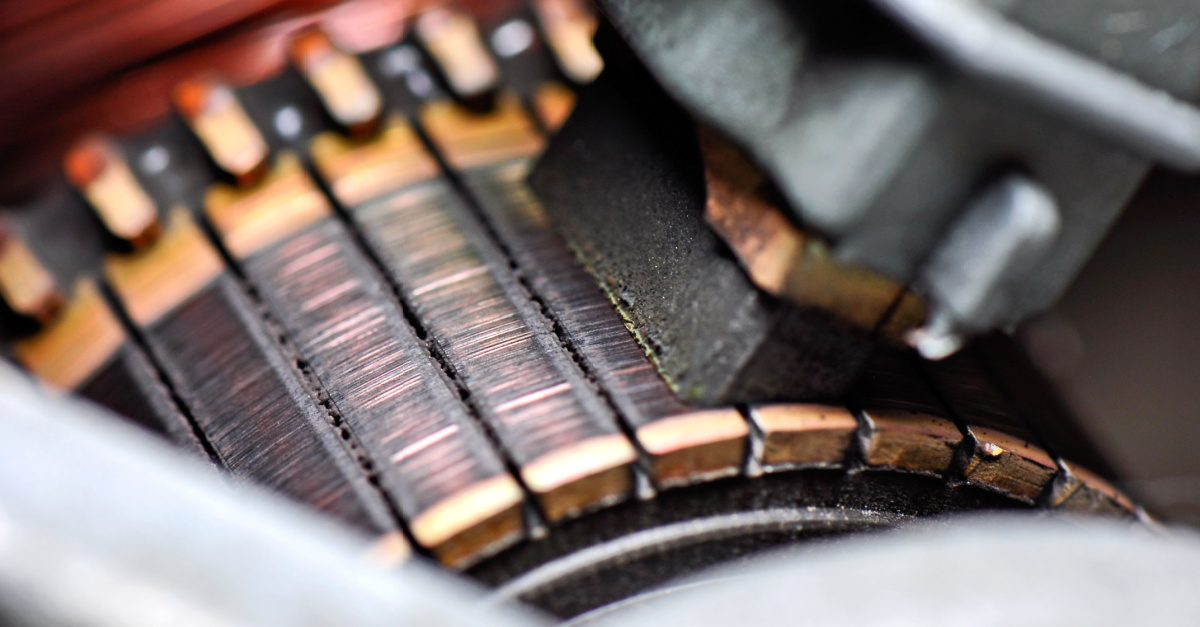
Maximising The Lifespan Of Carbon Brushes In Manufacturing Machinery
Carbon brushes are essential parts of the machinery that are relied upon within manufacturing operations. They help move electrical power between parts that stay still and parts that spin. The lifespan of carbon brushes depends on factors such as how the machine is used, the weight it handles, its speed, and the quality of the brushes. Maximising carbon brush lifespan is essential for optimising machinery performance.
What Are Carbon Brushes?
Carbon brushes are essential in electric motors and generators. They serve as links, connecting the parts that move with those that stay still in the machine. Their main job is to carry electrical power and make the machine move. They primarily transfer electrical current, facilitating the generation of mechanical motion.
As these brushes contact rotating components, friction and wear occur over time, requiring periodic replacement. Their susceptibility to wear emphasises the importance of strategic maintenance practices for sustained performance. According to topdealsonline.shop, if your tool starts to become slower or the motor starts to spark, it could be a sign that the carbon brushes need replacing.
Factors Influencing Carbon Brush Lifespan
The location where manufacturing machines operate significantly affects how long carbon brushes last. Manufacturers and machine operators must be aware of these points to implement effective strategies to make carbon brushes last longer in manufacturing machines.
Operating Conditions
The carbon brush uses and operating conditions are important considerations. Where manufacturing machines operate has a big impact on how long carbon brushes last. If the environment is too hot, humid, or dusty, the brushes wear out faster and might stop working.
To manage this, manufacturers should ensure good airflow, control the temperature, and clean things regularly. Doing these things creates a better environment, reducing the bad effects of heat, humidity, and dust.
Load and Speed
The workload and operational speed of machinery significantly affect the wear on carbon brushes. High loads and speeds increase friction, accelerating wear and reducing brush lifespan.
Adjusting load and speed within recommended limits contributes to prolonged brush life, balancing efficiency and preservation. This proactive approach enhances overall machinery performance and extends carbon brush lifespan.
Quality of Carbon Brushes
Carbon brush quality significantly influences their lifespan and impact on manufacturing machinery. Investing in high-quality brushes tailored to specific applications and electrical requirements improves wear resistance and conductivity, leading to longer-lasting performance.
Proper Brush Bedding
The bedding-in process of carbon brushes is crucial for their long-term performance in manufacturing machinery. Proper bedding-in is essential for minimising friction, heat generation, and premature wear. Adhering to manufacturer guidelines during this process is crucial to achieving optimal effectiveness and performance throughout the operational life of carbon brushes in machinery.
Strategies for Maximising Carbon Brush Lifespan
Making carbon brushes last longer in manufacturing machines is important for ensuring everything works well and doesn’t cost too much. This involves ensuring the machines operate in a suitable environment. Handle the right workload quickly, use high-quality brushes, and follow proper startup processes.
Regular Inspection and Maintenance
Checking and caring for carbon brushes in manufacturing machines is essential. This helps catch problems early, like when the brushes wear out or get damaged. Cleaning and changing the brushes as part of a proactive plan makes them last longer. This ensures machines work better, save money, and keep everything running smoothly.
Optimised Operating Conditions
Optimising operating conditions is crucial for extending the lifespan of carbon brushes in manufacturing machinery. This entails maintaining adequate ventilation, controlled temperature, and cleanliness to reduce friction and wear.
Monitoring and adjusting parameters, such as workload and speed, contribute to optimising conditions for carbon brush longevity. This prevents premature wear and failures and ensures sustained performance and efficiency in manufacturing machinery, leading to long-term benefits and reduced downtime.
Proper Lubrication
Proper lubrication is a potential solution for minimising friction and wear on carbon brushes in specific manufacturing applications. Adhere to manufacturer-recommended lubricants.
Precise application ensures optimal results in extending the lifespan of carbon brushes in machinery. Monitoring, adjusting, and incorporating lubrication into routine maintenance practices contribute to a practical and balanced approach.
Correct Brush Selection
Selecting the right carbon brushes is crucial for optimising the performance and lifespan of manufacturing machinery. Considerations include evaluating current capacity, wear resistance, and compatibility with operating conditions. Collaboration with knowledgeable suppliers and manufacturers is valuable in making informed decisions tailored to specific machinery needs.
Conclusion
Maximising the lifespan of carbon brushes in manufacturing machinery involves understanding wear factors and implementing effective maintenance strategies. By addressing operating conditions, workload, brush quality, and maintenance practices, manufacturers can enhance durability, optimising machinery performance. Ongoing brush materials and design research promises continuous improvements in carbon brushes’ lifespan, benefiting the manufacturing industry.
Upskill your manufacturing team with IoSCM. Call 0800 1422 522 today to find out more.