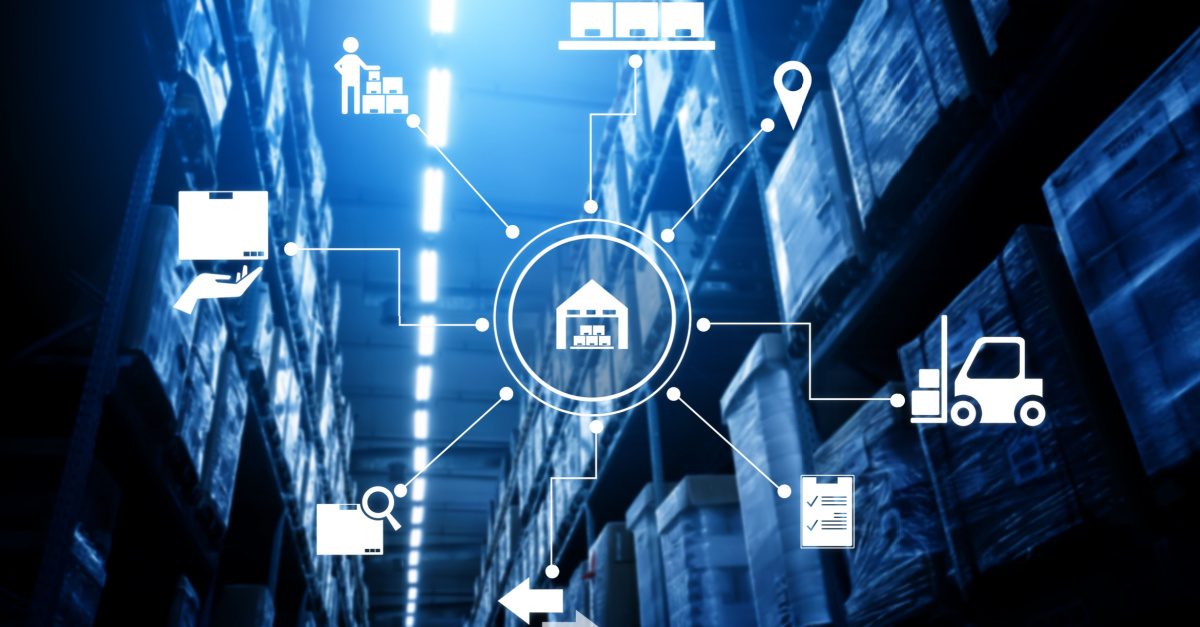
Implementing Vendor-Managed Inventory (VMI) for Supply Chain Optimisation
A company’s supply chain is critical as shareholders want maximum profitability and efficiency. Logistics professionals worldwide use different approaches for optimising the supply chain with varying outcomes. Vendor-managed inventory (VMI) is prominent because it reduces liability and ensures the best people do the job.
How can businesses implement VMI? Here’s a guide on using VMI for supply chain optimisation.
How to Implement VMI for Supply Chain Optimisation
Letting vendors control the supply can be a challenging transition for companies. Here are five ways to implement VMI successfully and ensure a fruitful endeavour.
Defining Objectives
First, companies must define their objective with VMI. This management technique has numerous types, so a business must determine which suits them.
For example, an electronics store may use a consignment inventory strategy to keep stock inside its building while letting the vendor own the materials. If an item goes unsold, the vendor can easily remove the product from the facility. This strategy is optimal for companies with products moving slowly.
A newer approach to VMI is the self-service strategy. This tactic gives clients more power and reduces the stress on inventory systems. With this enhanced visibility, buyers can see the demand forecasts, inventory levels and other data points before deciding.
Finding Trustworthy Partners
Relinquishing inventory control is no small feat, so finding trustworthy partners is essential for all parties involved. Researchers must do their due diligence and evaluate all options on the table. Which vendors have demonstrated the best results for their companies? Will the vendors adhere to expectations?
Communication should be the priority for companies and their vendors. Vendors should respond promptly to enquiries, support their partners and consistently prove their trustworthiness throughout the partnership.
Educating Employees
Employees are the heart of an organisation, so training them on new VMI practices is essential. First, they’ll need education on how VMI will change the workplace. Workers may be sceptical, so the training leads should illustrate real-world examples of VMI and successful implementation.
PepsiCo is an excellent example because of its VMI strategy. The food and beverage company watches its inventory at stores worldwide and efficiently manages its levels at each shop. Its careful inventory management has led PepsiCo to increase its profit forecast three times in the past year.
Incorporating New Technologies
Transitioning to VMI may require employees to learn new technologies. While older workers may have a more challenging time, this opportunity is excellent for professional development. A 2021 study finds 63% of workers left their jobs and cited lack of professional development as their primary reason.
VMI brings many technologies to companies. Inventory management software is the tip of the iceberg, but vendors also use the Internet of Things (IoT), cloud computing and other advanced services to retrieve the best possible information.
Monitoring Performance
Hiring vendors can be a significant financial investment for a company, so monitoring performance is crucial for continued success. The organisation should set key performance indicators (KPIs) and consistently track them throughout the company-vendor relationship. Companies should review factors like the inventory turnover rate, fill rate and order accuracy.
What Are the Benefits of VMI?
VMI can be challenging, but successful implementation comes with these three benefits:
1. Gaining Advantages
Shareholders expect their companies to be the best, so finding ways to improve is essential. Supply chain management is a way companies separate themselves from the pack. A survey finds 55% of business managers say supply chain management is the best way to provide a competitive advantage. VMI gives companies a leg up by reducing inventory costs and becoming more efficient.
2. Increased Accuracy
VMI simultaneously lowers the risk and increases the accuracy for companies. The risk goes down because they’re more capable of forecasting demand and adjusting their supplies accordingly. With VMI, organisations and their vendors have increased transparency and are better able to respond when sudden shifts in demand occur. The last thing a company needs is stockouts or overstock and angry consumers.
3. Satisfying Customers
VMI lowers the risk of products being out of stock, thus satisfying customers and increasing their happiness with the business. The past few years have demonstrated significant supply chain issues and stockouts, leading to customer confusion and complaints. Research shows 56% of online shoppers could not purchase products due to stockouts.
What Challenges Come With VMI?
While VMI brings benefits, it can challenge companies if proper implementation does not occur. Organisations should be wary of these three drawbacks:
1. Implementation Costs
With tight budgets, companies may need help implementing VMI. This inventory management tactic requires training, new technology and transition time into the new system. Some organisations can quickly change to VMI, but not every business can. Companies wary of the costs should anticipate VMI’s long-term pros and cons.
2. Reduced Control
Relinquishing control is one of the biggest challenges with VMI. While VMI can be advantageous, companies add risk by taking losses on their inventory. The vendor could miscalculate demand and leave warehouses overstocked or undersupplied to meet customer requests. Additionally, the company must worry about vendors using unapproved practices, outdated technology and other liabilities.
3. Cybersecurity Concerns
The chosen vendor could have lax cybersecurity practices, leading to concerns for all parties involved. Companies must ensure the vendor employs strong cybersecurity methods, or else they risk cyberattacks and significant financial ramifications. Research shows human error causes 95% of cyberattacks, so being strict with data is crucial.
Implementing VMI for Improved Outcomes
The world has put supply chains under a microscope in the past few years, so companies must optimise their business practices as much as possible. VMI is one strategy organisations take to improve their demand forecasting, control inventory levels and save money. Companies with the means should evaluate the pros and cons and consider these implementation strategies.
Author Bio
Jack Shaw, senior editor of Modded, is a respected authority on industry and business strategies. With a deep understanding of supply chains and a talent for breaking down complex concepts into easily digestible insights, Jack’s articles offer a fresh perspective on current trends and processes.
Advance your warehouse and inventory management capabilities with IoSCM. Call 0800 1422 522 to find out how we can help.