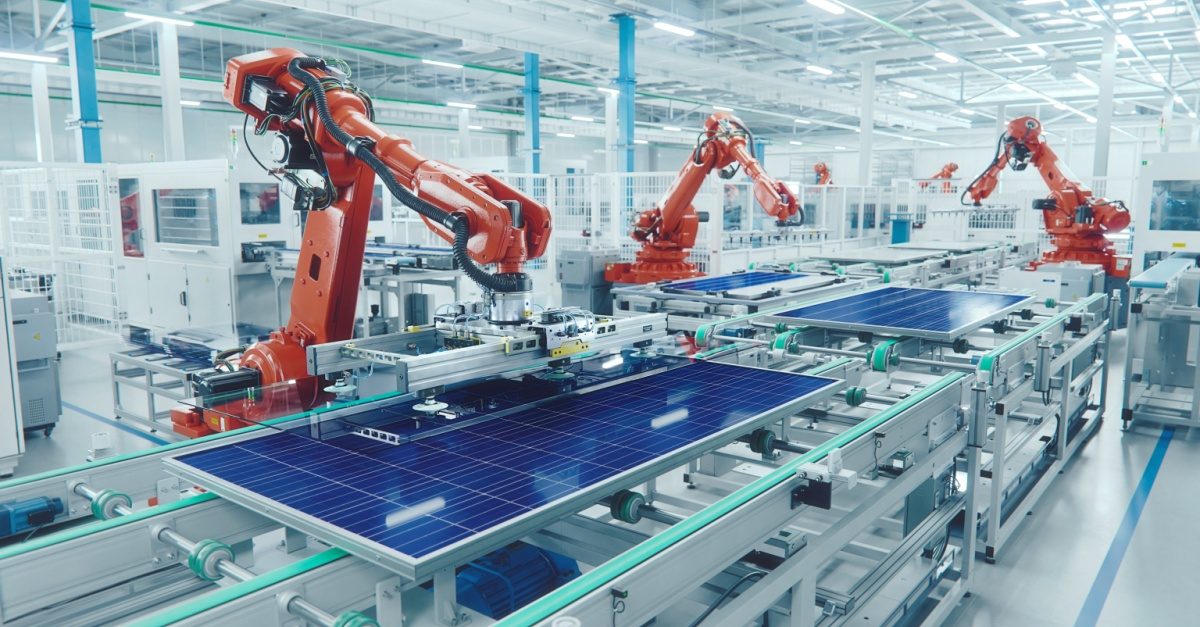
Manufacturing Insights: How To Optimise Fluid Handling Systems In Factories
Fluid handling systems are crucial in many manufacturing industries, requiring not just implementation but also an optimised design for maximum efficiency. Enhancing these systems can lead to a more efficient overall facility operation, with reduced waste and increased longevity. To improve facility operations and decrease time and product losses, upgrading fluid handling equipment is advisable. Modern components are built for durability, promoting longer-lasting systems and boosting productivity and efficiency.
Optimising fluid handling systems is paramount for factories aiming to enhance efficiency, reduce operational costs, and maintain compliance with environmental standards. A well-tuned fluid handling system not only conserves resources but also improves production quality and safety. This article explores key strategies to optimise these systems effectively.
Conducting Systematic Audits and Assessments
The first step in optimisation is thorough system auditing and assessment. Regular inspections should be mandated to check the integrity of pipes, pumps, valves, and tanks. Early identification of issues such as leaks, corrosion, or inefficiencies can prevent costly repairs and downtime later. Incorporating flow measurement and monitoring tools can provide real-time data on flow rates and pressure, facilitating proactive maintenance and adjustment.
Investing in high-efficiency equipment can lead to significant energy savings and operational improvements. Modern pumps and motors typically offer better performance and consume less energy. Additionally, automating fluid handling with smart valves and sensors can enhance the precision and responsiveness of the system, allowing for real-time adjustments and reducing human error. Learn more about how Asco implements fluid automation solutions to maximise customer efficiencies, optimise applications, and improve safety.
Improving Piping and Valve Management
Optimising the layout of pipes by minimising bends and reducing the length of runs can significantly decrease pressure drops and energy use. It is crucial to maintain valves and seals in good condition to prevent leaks that could lead to system failures and safety hazards. Regular maintenance checks and timely replacements are essential components of an effective fluid management strategy.
Enhancing Energy Efficiency
Enhancing energy efficiency in fluid handling systems can be significantly achieved by integrating Variable Frequency Drives (VFDs) and installing heat recovery units. VFDs adjust motor speeds according to demand, reducing energy consumption and mechanical wear, thereby extending equipment lifespan.
Heat recovery units capture and reuse waste heat from high-temperature fluid streams, decreasing the energy needed to heat incoming fluids and reducing carbon emissions. Although these technologies involve initial investments, the long-term benefits of lowered operational costs and improved sustainability make them essential for modernising industrial fluid handling systems and adapting to eco-friendly operational standards.
Managing Fluids Intelligently
The quality of the fluids used plays a critical role in system performance. Regular testing and appropriate treatment help prevent issues like scaling and corrosion. Additionally, choosing the right fluids that meet the specific needs of the system while considering environmental conditions can extend the life of the equipment and improve efficiency.
Integrating Systems
Where possible, fluid handling systems should be integrated with other process systems within the factory. This integration can lead to better coordination, reduced waste, and enhanced efficiency. Using advanced simulation software to model fluid dynamics can help identify inefficiencies and potential improvements in the system design.
Fostering Skilled Workforce
Operational staff should receive ongoing training on the latest operational and maintenance practices. A well-informed team can operate the system more efficiently and is better prepared to handle emergencies. Developing standard operating procedures (SOPs) for regular and emergency operations can ensure that the systems are managed consistently and efficiently.
Adopting Sustainability Practices
Choosing environmentally friendly fluids and implementing recycling or proper disposal practices for spent fluids can minimise the environmental impact of the factory. Such practices not only comply with environmental regulations but also improve the public image of the company.
Leveraging Advanced Technologies
Emerging technologies can be harnessed to optimise fluid handling systems further. Internet of Things (IoT) devices can provide comprehensive monitoring and generate large data sets that, when analysed with artificial intelligence (AI), can predict system failures, optimise maintenance schedules, and improve system configurations.
Regular Review and Continuous Improvement
Optimisation is not a one-time task. It is a continuous process. Regularly reviewing the performance of the fluid handling system against set benchmarks can highlight areas for further improvement. Implementing a cycle of constant improvement based on the principles of Lean and Six Sigma systematically reduces waste and inefficiency.
Conclusion
Optimising fluid handling systems in factories is a multifaceted endeavour that requires a strategic approach encompassing equipment upgrades, system integration, skilled workforce development, and the adoption of new technologies. By implementing these strategies, factories can achieve significant gains in efficiency, cost reduction, and environmental sustainability. The journey towards optimisation is ongoing, and staying abreast of industry best practices and technological advances is essential for maintaining competitive advantage and operational excellence.
Modern Manufacturing requires skilled, capable and enthusiastic team members to deliver sustainable operations that meet the needs of the business and the wider supply chain. Upskill your manufacturing team and your manufacturing operations with IoSCM. Call 0800 1422 522 option 2 to speak with the IoSCM Corporate Team today.