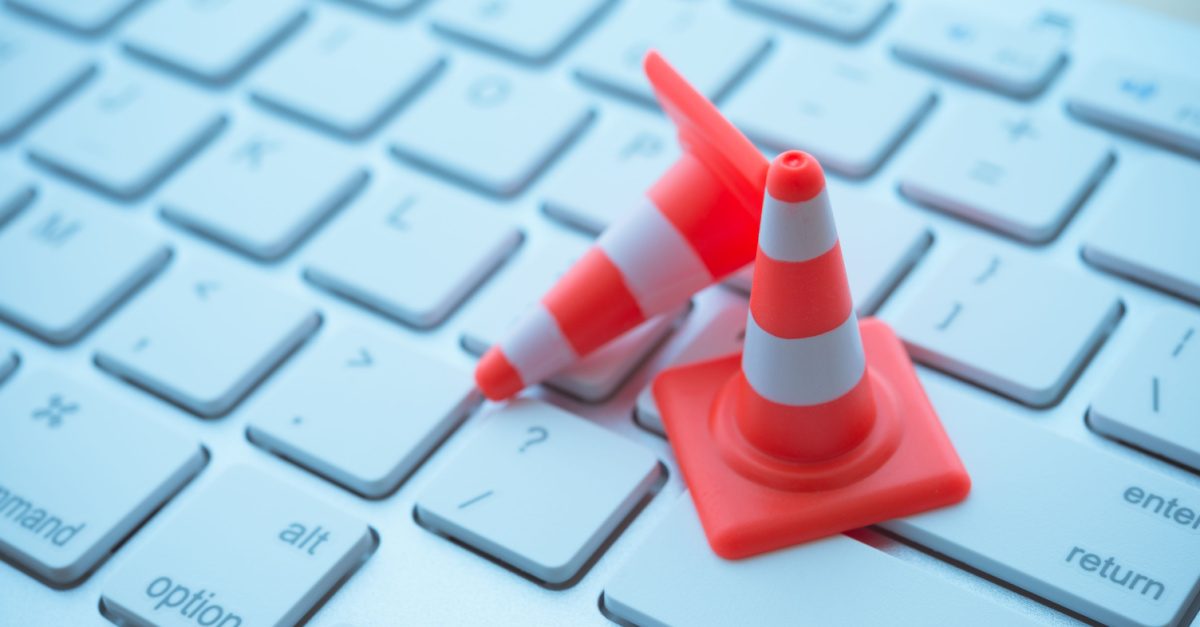
Five Best Practices In Preventive Maintenance Scheduling
Preventive maintenance scheduling involves strategic planning and smart decision-making. It’s not just about setting reminders for maintenance tasks. Instead, it’s about creating a holistic approach to maintaining your equipment that can significantly reduce unexpected breakdowns. This article will explore the best practices in preventive maintenance scheduling. We’ll discuss effective strategies to streamline your maintenance processes, boost efficiency, and prolong the service life of your assets.
Use Software Solutions To Streamline Processes
In the digital age, leveraging software solutions can be crucial in optimising your preventive maintenance scheduling. This could include using a variety of tools that help automate scheduling, issue timely reminders for maintenance tasks, and securely store data on equipment history.
One such tool that can significantly enhance the maintenance process is job management software. By integrating this software, businesses can bring a structured approach to task organisation, resource allocation, and overall project management.
Using software solutions in tandem with traditional preventive maintenance methods can lead to a more streamlined and efficient maintenance process. This ensures that no task or piece of equipment is overlooked, ultimately leading to improved efficiencies and a higher rate of preventive maintenance success.
Prioritise Based On Criticality And Condition
Maintaining an organised maintenance schedule can be a daunting task. When faced with a long list of equipment to maintain, it can be easy to lose sight of where to begin. However, this can be addressed effectively by prioritising. Here are two factors to consider:
- Criticality Of Equipment: Prioritise equipment that plays a crucial role in your operations. If a particular machine’s failure would disrupt your services significantly, it deserves a higher priority.
- Current Equipment Condition: Consider the present state of your equipment. Older or frequently-used machines may require more regular maintenance than newer or infrequently-used ones.
By focusing on the equipment’s criticality and condition, you effectively prioritise essential assets. Having determined what needs attention, let’s consider the optimal timing for these maintenance tasks.
Leverage Predictive Maintenance Technologies
Moving from a reactive to a proactive maintenance strategy can significantly reduce unplanned downtime. The cornerstone of this strategy is predictive maintenance technologies. By identifying potential issues before they become significant problems, you can schedule maintenance when it’s needed most.
Here are a few predictive maintenance technologies to consider:
- Vibration Analysis: This technique can detect abnormalities in rotating equipment like pumps, motors, or fans.
- Infrared Imaging: Thermal imaging can identify hotspots in electrical equipment, which often indicate a looming failure.
- Oil Analysis: Regular oil analysis can detect contaminants or changes in viscosity, which can signal issues in machinery like engines or hydraulic systems.
Having addressed ‘what’ and ‘when’, let’s move on to ‘who’ and the significance of team training.
Train Your Team
A preventive maintenance programme’s success relies heavily on the team executing it. Even the best preventive maintenance scheduling can falter without a well-informed and skilled team.
Consider the following when training your team:
- Technical Training: Ensure that your team is adept at handling the specific equipment and technology they will be working on. This includes knowledge of predictive maintenance technologies and proper use of your CMMS.
- Preventive Maintenance Principles: Beyond technical skills, your team should understand the fundamental principles and importance of preventive maintenance. This will empower them to make informed decisions in their daily tasks.
A highly trained team is essential for effective preventive maintenance. However, they also need a flexible and up-to-date plan to work with.
Review And Update Your Preventive Maintenance Schedule:
A preventive maintenance schedule isn’t a document you create once and then forget about. Instead, it’s a dynamic tool that should adapt to your business’s changing needs. Therefore, it’s crucial to regularly review and update your schedule based on factors such as:
- Equipment Usage Changes: If equipment usage increases or decreases significantly, the maintenance schedule may need adjusting accordingly.
- Feedback From Maintenance Team: Your team’s insights and experiences from carrying out maintenance tasks can provide valuable input for schedule adjustments.
Regularly reviewing and updating your schedule ensures your preventive maintenance remains relevant and effective.
Conclusion
Preventive maintenance scheduling is a powerful tool that, when implemented correctly, can significantly improve your operations. It might sound challenging, but the rewards – reduced downtime, extended asset life, and increased operational efficiency – are indeed worth the effort.
Remember, every business is unique, and what works best for one might not be the best for another. Take the time to understand your operational needs, explore different strategies, and don’t be afraid to adapt and change.
After all, successful preventive maintenance scheduling isn’t a one-time task but an ongoing process. With persistence and the right approach, you’ll be on your way to mastering preventive maintenance scheduling in no time.
Preventive Maintenance is just one way you can ensure the lifespan of your operations. Skilled employees, a talent pipeline, and industry know-how are three other great ways to stay competitive! Find out how an IoSCM Professional Qualification can help. Call 0800 1422 522 today.