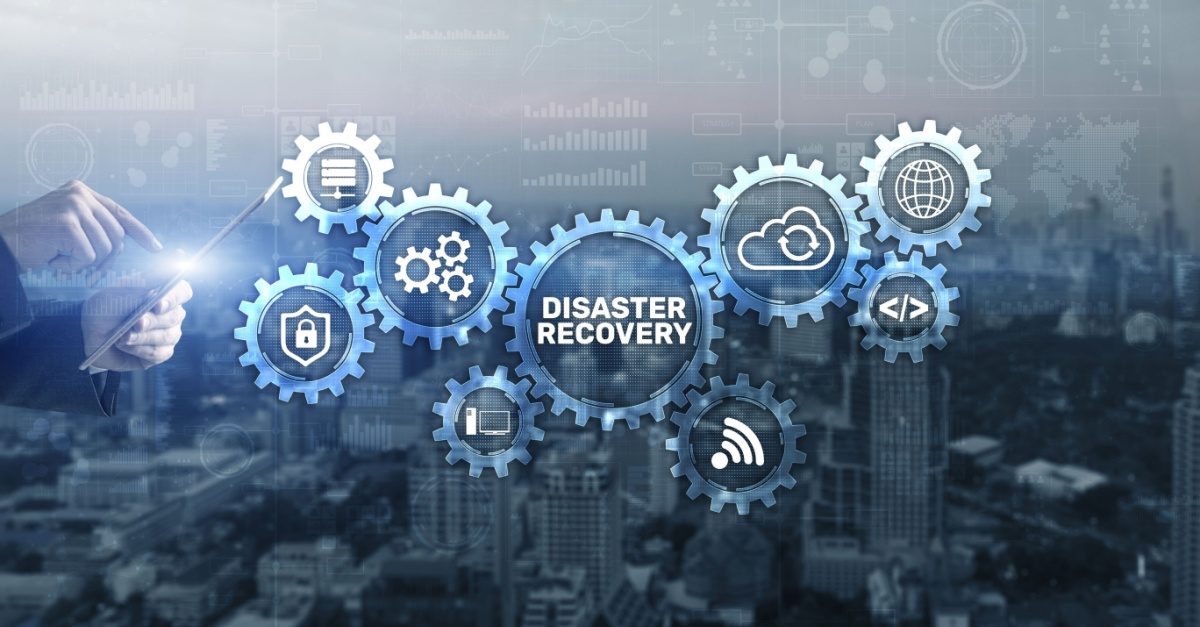
10 Tips For Disaster Recovery In Precision-Driven Industries
Precision-driven industries such as aerospace, pharmaceuticals, biotechnology, and advanced manufacturing, rely on highly specialised equipment and stringent quality control measures. However, even the most meticulously managed operations are not immune to disasters—whether natural, technological, or human-induced. This article explores essential tips for effective disaster recovery in such high-stakes environments, ensuring resilience and continuity in the face of adversity.
1. Establish Strong Partnerships with Suppliers and Vendors
Establishing strong relationships with key partners and developing contingency plans with them can mitigate this risk. For example, in the automotive industry, where just-in-time manufacturing is common, having alternative suppliers for critical components can prevent production delays during a disaster.
Similarly, industries requiring precise liquid handling, such as pharmaceuticals or biotechnology, can benefit from partnering with experts at Pipette, who provide reliable air displacement pipettes that ensure precise dispensing of liquids. These tools align with stringent standards and support innovative solutions to meet the exact specifications critical to maintaining standards of quality in research and production processes.
2. Develop a Comprehensive Disaster Recovery Plan
A robust disaster recovery plan (DRP) is the cornerstone of resilience in precision-driven industries. This plan should outline clear protocols for responding to various types of disasters, including natural events (e.g., earthquakes, floods), cyberattacks, equipment failures, and human errors.
The DRP must be tailored to the specific needs of the industry, accounting for the unique challenges posed by precision requirements. For example, in pharmaceutical manufacturing, even a minor deviation in temperature or humidity during recovery could compromise product quality.
For organisations leveraging cloud platforms like Azure, partnering with Atmosera’s DR experts can provide comprehensive disaster recovery solutions tailored to Azure environments. Their expertise ensures seamless recovery processes, minimising downtime and maintaining operational precision, even in the face of unexpected disruptions.
3. Leverage Redundant Systems and Backup Solutions
Implementing redundant systems—such as backup power supplies, duplicate machinery, and failover servers—ensures that operations can continue seamlessly in the event of a failure. Additionally, maintaining off-site backups of critical data and digital systems is essential for quick recovery.
For example, in aerospace manufacturing, where computer-aided design (CAD) files and precision measurements are vital, cloud-based backups can provide immediate access to essential data, even if on-site systems are compromised.
4. Invest in Advanced Monitoring and Predictive Maintenance
Advanced monitoring systems, powered by IoT sensors and artificial intelligence (AI), can detect anomalies in real time, allowing for proactive interventions before a minor issue escalates into a disaster. Predictive maintenance relies on data analytics to identify potential equipment failures, helping to minimise unexpected downtime.
For instance, in semiconductor manufacturing, where nanoscale precision is required, even a slight deviation in equipment performance can lead to defective products. Predictive maintenance ensures that machinery is always operating at peak performance.
5. Train Employees for Disaster Scenarios
Human error is a leading cause of disruptions in precision-driven industries. Well-rounded training programs give employees the skills and know-how to handle emergencies confidently. This includes technical training, drills, and simulations to familiarise employees with recovery protocols.
In biotechnology, where sterile environments are critical, employees must be trained to maintain precision even under stressful conditions. Practicing drills regularly helps team members remember the right steps and spot problems in the disaster recovery plan.
6. Prioritise Cybersecurity Measures
A breach can compromise sensitive data, disrupt operations, and even sabotage equipment. Implementing robust cybersecurity measures, such as firewalls, encryption, and multi-factor authentication, is essential for protecting critical systems.
Regular security checks and testing can find and fix weaknesses before hackers can take advantage of them. Having a team ready to handle cyber threats helps respond quickly and effectively when problems arise.
7. Conduct Regular Risk Assessments
Regular risk assessments identify emerging threats and vulnerabilities, ensuring that your disaster recovery plan remains relevant and effective. This is particularly critical in industries driven by precision machining and cutting-edge technologies, where continuous innovation and evolving stringent standards can introduce new risks.
For example, in the pharmaceutical industry, changes in regulatory requirements may necessitate updates to disaster recovery protocols to ensure compliance with exact specifications and standards of quality. Similarly, industries relying on art power transmission products or abrasive products must adapt their strategies to address risks introduced by advancements in art technology and innovative solutions.
8. Ensure Clear Communication Channels
Establishing clear communication channels, both within the organisation and with external stakeholders, is vital for a coordinated response. This includes implementing backup communication systems, such as satellite phones or radio networks, to ensure continuity if primary systems fail.
In industries like aerospace, where versatile capabilities and tight tolerances are paramount, clear communication ensures that all teams remain aligned during recovery efforts. This innovative approach to communication is equally important in the product development process, where collaboration across teams is essential to move seamlessly from concept to creation.
9. Document Lessons Learned
Conducting a post-disaster review to document lessons learned is a critical step in refining your disaster recovery plan. This process should include an analysis of what worked well, what didn’t, and what could be improved.
For instance, in the event of a power outage at a facility specialising in precision machining or boring products, documenting the response can highlight areas for improvement, ensuring better preparedness for future disruptions. This practice aligns with the product lifecycle approach, where continuous feedback and refinement are key to maintaining quality air products and other high-standard outputs.
10. Adopt a Culture of Resilience
Building a resilient culture involves fostering risk awareness, promoting proactive problem-solving, and empowering employees to stay prepared. In industries that rely on cutting-edge technologies and innovative solutions, a resilient workforce is essential for navigating challenges and ensuring rapid recovery from disruptions.
This culture of resilience is particularly important in the design process and approach to product development, where adaptability and preparedness are critical to meeting stringent standards and delivering wide range solutions.
Bottom Line
Disaster recovery in precision-driven industries is a complex and multifaceted challenge that requires careful planning, advanced technology, and a commitment to continuous improvement. Consulting with industry experts can provide tailored solutions and strategic insights to ensure your disaster recovery plan is robust, efficient, and aligned with the unique demands of your operations.
Want to achieve operational excellence? Talk to IoSCM about how professional qualifications, corporate membership and our industry-leading expertise can help you achieve your strategic objectives. Call 0800 1422 522 today.