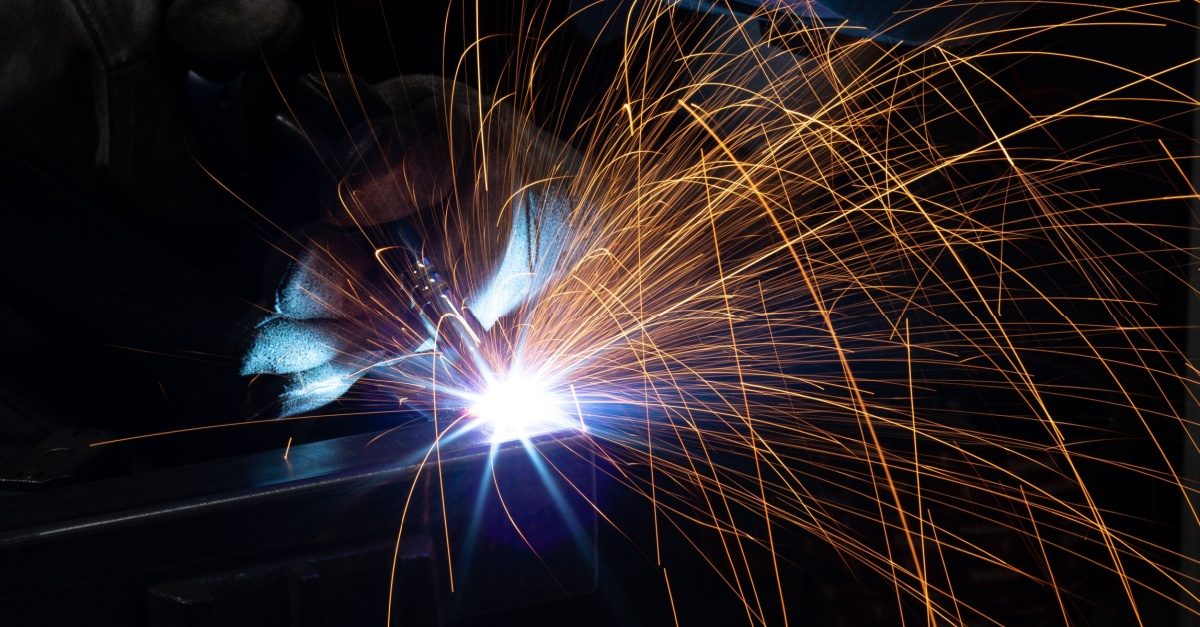
Using Stud Welding Techniques to Improve Sustainability in the Supply Chain.
Welding is an integral aspect of a manufacturing and production process in a wide range of industries. So, how can we ensure that this technique is optimised for sustainability in the supply chain?
Welding is a process of generating heat to melt metals, attaching them together to form a strong bond. There are several different welding techniques available to produce a finished weld. Each technique uses a unique process and has its own environmental considerations. Before looking at Stud Welding in more detail we need to understand the environmental considerations of any type of welding.
What environmental factors are there to consider with welding?
When welding, energy is used to produce electricity and heat and consumables are used in the process with potential waste left behind. Manufacturers should consider the quantity of material waste, the efficiency of the process, how energy consumption can be minimised and the emissions released into the environment.
How does the stud welding process help to achieve sustainability goals?
Material Quantity
Stud welding structures are simplified versus other welding methods giving real material savings. Stud welding allows the user to save on their parent material, the sheet that they are welding onto.
There are many applications that this applies to. In general panelwork fabrication, equivalent welding methods would require a substantially greater material thickness in order to allow for the drilling, tapping or to backweld in a countersunk screw. This would normally require a material thickness of 3-5 mm depending on the diameter. However, with stud welding it is possible to achieve a fixing on parent material of 1 mm and under! This saves not only on material thickness, but also on waste from drilling, production costs and time.
Material Wastage
Producing less waste helps to make the process more sustainable by minimising the disposal of waste materials which lead to emissions in the environment. Instead of saving through thinner materials, drawn arc stud welding allows for reduced material wastage by omitting offcut materials. As stud welding eliminates the requirement for any drilling, tapping, punching or rivetting which are needed in other types of welding processes, it means there’s no waste leftover.
Energy Consumption
When comparing the typical power consumption of various welding machines, stud welding is the most efficient. Capacitor Discharge machines use around 3000 watts to charge for 1 weld. Comparatively, MIG consumes approximately 2000-8000 watts per second of weld time. As the weld time for MIG is considerably longer than stud welding, comparatively it consumes a greater amount of power to complete the weld.
Capacitor discharge stud welding machines usually charge single phase between 5-13 Amps. They use low power dissipation, meaning economical energy consumption. Traditional welding methods (when considering comparative industrial welding) require a small 3 phase power supply of 16-32 Amps.
Welding Efficiency
The stud welding process is considerably more time efficient than other methods. For example, welding a bolt with a MIG welder takes around 45-60 seconds. Throughout this time, energy is used continuously to execute the weld. Comparatively, a stud welding machine completes the majority of welds in less than 1 second, with the CD machine rapidly welding a stud in 5 milliseconds.
Whilst both types of welding use an intense amount of energy during the welding process, stud welding’s speed means that the overall energy consumed per weld is significantly lower than other methods. Quicker weld + less charging time = lower energy usage.
How does stud welding compare against other welding methods when it comes to consumables?
Consumables like drill bits and parent materials are used in the welding processes. As well as minimising material quantity, stud welding doesn’t require the use of drill bits as the process does not include any incision into the material. Stud welding produces a stronger weld than other methods as a result too (as drilling or cutting the parent material will weaken its composition). As well as saving on consumables, this is beneficial to manufacturers as it also saves on costs.
Other welding techniques, MIG and TIG welding, use additional consumables including wire and shielding gases that are not needed for stud welding. In addition, users don’t face the extra environmental impact of shielding gas emissions, gas bottle storage and transportation and the associated supply chains. Stud welding’s minimal use of consumables makes the process more sustainable than other types of welding.
Sustainable Suppliers
When selecting materials and equipment, manufacturers should consider a supplier’s sustainability processes. To maximise sustainability through stud welding, you should ensure that the stud welding machine manufacturers are optimising their production methods for sustainability. Look for supplier certifications including ISO 14001:2015 to ensure that your provider is adhering to high standards of environmental management. Leading UK stud welding manufacturers, Taylor Studwelding, are a great example of a sustainable company that are investing in maximising sustainability in their production line to aid the overall supply chain.
Other benefits of using stud welding in the supply chain
Stud welding is not only beneficial for its environmentally friendly qualities, it’s also used as a preferential welding method for:
- Ease of use
- Uniform welding quality
- Strength of welds
- Versatility on a wide range of materials.
- No leakage through joints.
- No machining required after welding on the exposed side.
Author – Andrew Gillings, Taylor Studywelding Systems Ltd.
With decades of experience, Andrew is a hands-on and dedicated Sales Manager at Taylor Studwelding Systems. Joining the company in 2004, Andrew has built a profound technical understanding of stud welding processes, as well as extensive product knowledge. He consults with clients from a wide range of industries both locally and internationally, helping them find innovative and efficient solutions for their project needs.
Company Bio
Taylor Studwelding Systems Ltd. is the UK’s sole manufacturer and distributor of stud welding equipment and accessories, including, capacitor discharge (CD) and drawn arc (DA) stud welding machines, weld studs and CNC equipment. Taylor Studwelding has a global reputation as a top supplier, designer and manufacturer, continually investing in R&D to bring new, modern and sustainable stud welding products to the market. Visit our website to find out more – https://www.taylor-studwelding.com/