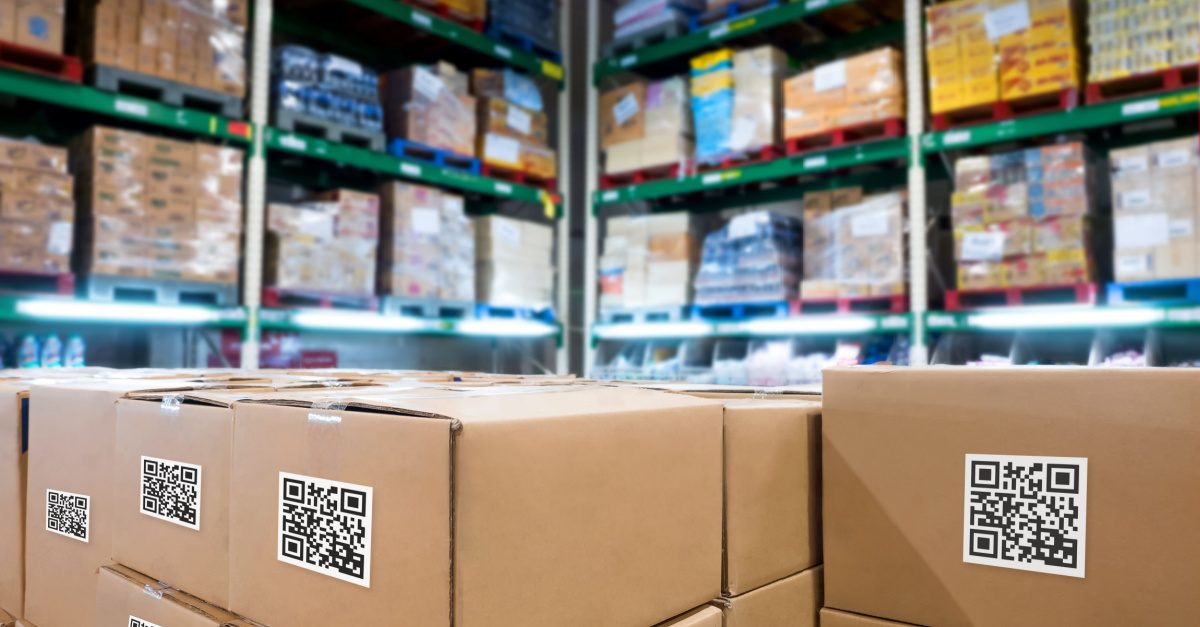
Implementing Voice-Picking Systems for Improved Accuracy in Warehousing
Voice-picking has become one of the most important components of warehouse automation and optimisation in recent years. Paperless and hands-free selection systems with simple voice prompts are ideal for combating modern supply chain challenges and ensuring accurate order fulfilment. Here are the benefits of voice-picking systems and how manufacturing professionals can implement them in their warehouse operations.
Improved Accuracy
Order fulfilment has gotten faster and more complex, and consumers can receive goods as quickly as the next business day. Picking is the most expensive part of warehouse operations and is usually where the most inaccuracies occur. A paper-based process is always slow and mistake-prone when humans are doing the paperwork.
Voice-picking combines headsets, microphones and mobile devices with speech recognition into existing warehouse management systems. It replaces radio-frequency identification (RFID), barcode scanning, and paper-based order selection with a quick and straightforward communication process.
A voice-based selection method ensures order accuracy by verifying each item’s characteristics and quantity through verbal confirmation. Making employees provide clearly spoken directives and real-time feedback instead of written instructions decreases the chances of an entry mispick or misinterpretation.
These systems can achieve an accuracy level of up to 99.99% in warehouses and distribution centres. Even large warehouse operations can decrease their error rates after switching to voice-picking systems.
Increased Productivity
Voice-picking systems also improve warehouse productivity thanks to their hands- and eyes-free operation. Instead of filling out paperwork or manually entering product information into a computer, workers can communicate verbally and thus devote more attention to their picking tasks.
Another way that voice-picking systems improve productivity is by helping employees create optimised paths and directing them to exact workplace locations. Warehouses and distribution centres are thousands of square feet and have hundreds of shelves. Voice-picking systems provide an outlet for workers to guide each other through these cluttered environments.
Voice-picking systems can boost productivity by up to 35%, according to some businesses that have made the switch. This percentage will vary based on the workplace’s size and number of employees. However, any warehouse operation can benefit from moving toward voice-picking instead of written or typed order fulfilment.
Enhanced Workplace Safety
Voice-picking systems enhance workplace safety by eliminating unnecessary handheld devices. Hands-free operation is one of the simplest ways to eliminate distractions and streamline workflows in dangerous environments like warehouses, manufacturing plants and distribution centres.
Voice-picking technology lets workers focus on their surroundings and handle items with both hands, reducing the risk of damage and injury. There are also ergonomic benefits, as employees don’t have to strain themselves from handling paperwork, radios and scanners all day.
4 Key Implementation Steps
Voice-picking solutions are highly adaptable to different warehouse needs, but it’s still crucial to consider the potential challenges of making the switch. For example, one issue many companies face is ensuring accurate voice recognition among diverse workforces. Business leaders should follow these four implementation steps to make employees comfortable with the change and ensure a smooth transition.
1. Assessing Warehouse Readiness
The first step in transitioning to a voice-picking system is to thoroughly analyse the warehouse’s layout, infrastructure and existing order fulfilment technologies. This initial assessment evaluates the new system’s compatibility and identifies potential integration challenges.
Ideally, the current warehouse management system and enterprise resource planning software will accommodate voice-picking without issue. Today’s advanced database management systems include predefined user interfaces that allow them to exchange data with new systems. Voice-picking integration should be a breeze in an up-to-date warehouse setting.
2. Finding the Right System
The next step is the research phase, in which the company compares different voice-picking system providers based on their technology offerings and track records. Some of the most important features in today’s diverse workforce include multi-language support, mobile device compatibility and noise cancellation for loud work environments. Managers should examine the pros and cons of multiple systems to find one that will work best in their warehouses.
3. Training Employees
Before introducing the new system, businesses must develop a detailed training programme that covers voice-picking functionality, proper command techniques and basic troubleshooting instructions. It must include hands-on activities so employees can practise their verbal commands and get comfortable with the system in a controlled environment. Ensuring workers are satisfied with the system is vital for its success.
4. Ongoing Monitoring and Learning
Managers must continue monitoring performance, gathering feedback and identifying learning opportunities once the system is in place and employees are using it daily. Data analytics comes into play, where key metrics like order selection accuracy, productivity levels and worker satisfaction are of utmost importance. Problems should be dealt with sooner rather than later to make the most of the new system.
Make the Switch to Voice-Picking Systems
Although voice-picking systems depend on employees making clear verbal commands, this order fulfilment method is still more accurate, productive, and safe than written or typed instructions. All managers of warehouses, manufacturing plants or distribution centres should reevaluate their current operations and switch to voice-picking as soon as possible.
Author Bio
Jack Shaw, senior editor of Modded, is a respected authority on industry and business strategies. With a deep understanding of supply chains and a talent for breaking down complex concepts into easily digestible insights, Jack’s articles offer a fresh perspective on current trends and processes.
Your warehouse operations need to be effective and streamlined to meet the expectations of your wider supply chain and customer base. IoSCM can help you develop the skills and knowledge of your entire team to drive positive results within your business. Call 0800 1422 522 today to find out more.