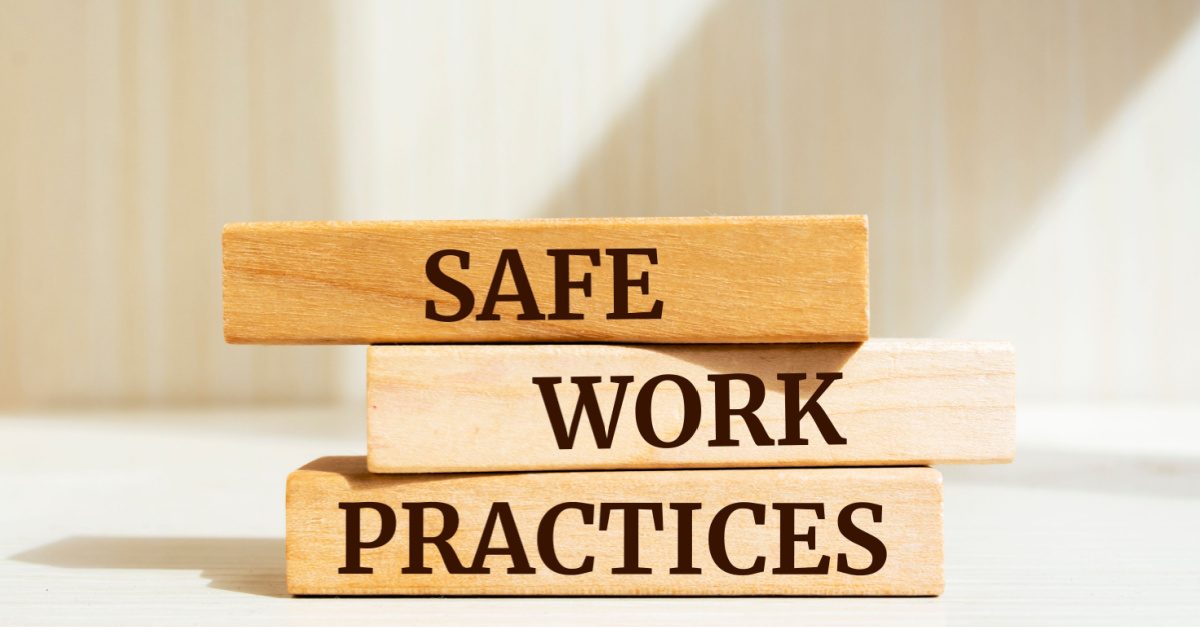
How Manufacturers Can Prevent On-the-Job Injuries in their Manufacturing Plant
Every good business leader knows that a company is nothing without its employees. Your workers are the life’s blood of your business. For that reason, prioritising employee safety is, or should be, job one. This is particularly true for workers in the manufacturing industry, where safety risks, unfortunately, abound.
Despite the myriad of hazards inherent to manufacturing jobs, it is possible to mitigate the risks of work-related illness and injuries. This article describes strategies business leaders can use to protect workers in the manufacturing industry, regardless of their particular job function.
Holding Regular Safety Training
When it comes to employee safety on the job site, one of the first and most important things managers and supervisors can do is ensure that workers are up to date on their safety training.
Regular safety training helps to ensure not only that all staff are familiar with the latest standards, regulations, and requirements, but also that they do not become complacent in regard to familiar safety protocols. The core mission of routine, comprehensive safety training is prevention, and promotion of a culture of workplace safety for all employees in all job roles and at every level of experience.
Reducing Exposure to Harmful Substances
The manufacturing industry is inevitably one in which workers are exposed to an array of potentially hazardous and even lethal substances. It’s critical that employees be educated both on the necessity of wearing personal protective equipment (PPE) at all times when handling or being exposed to harmful substances and on how to put on, wear, remove, and dispose of PPE safely.
It’s also essential that potentially harmful substances be stored and transported safely to reduce the risks of environmental contamination or toxic human exposure. This should include proper labelling and containment, as well as limiting access to only authorised personnel.
Mandating Safety Gear
In addition to ensuring that workers consistently and correctly wear the appropriate PPE when exposed to hazardous substances, it’s also vital that employees be mandated to wear other essential safety gear.
For example, concussions are a common injury for workers in the manufacturing industry, an injury that can lead to significant, long-term damage. However, these potentially debilitating injuries can often easily be prevented just by requiring everyone on a job site to wear a hard hat at all times.
Similarly, gear such as protective eyewear, steel-toed shoes, and earplugs can prevent short-term injury and long-term damage. Eyewear and hard boots, for instance, can prevent penetrating injuries, contusions, or fractures. Earplugs and muffs, likewise, can prevent tinnitus and hearing loss.
Allowing Rest Time When Needed
One of the greatest risks to your employees’ safety is, in fact, fatigue. If your employees are overworked or sleep-deprived, they’re far more likely to make a mistake that could lead to a catastrophic injury.
This is why it’s imperative that employees be given ample opportunities to rest when needed. Effective time management can facilitate this, enabling you to schedule sufficient break time without jeopardising manufacturing timelines.
Don’t Rush Employees
Much in the same way that ensuring employees have sufficient rest helps to prevent injuries, so, too, does avoiding the temptation to drive workers to meet unreasonable deadlines or production quotas. If your employees feel rushed, they’re going to cut corners and, in many cases, the first shortcuts will be those surrounding safety.
Instead, focus on techniques that will make workflows more efficient, such as keeping a well-organised and tidy warehouse, to help prevent your employees from becoming harried and, consequently, careless in regard to safety.
Avoid Repetitive Motions
Many manufacturing jobs require repetitive motion and, as such, injuries related to these motions are particularly common. Repetitive motion injuries can affect the spine, the hands, the muscles, and the joints in devastating ways, leading both to severe pain and loss of function. However, by varying workers’ job duties, you can reduce the risk of repetitive motion injuries.
And, as a bonus, when you rotate workers, you end up with more versatile and skilled employees and a workforce that is more agile and adaptive, enabling you to more easily adapt to worker absences or other contingencies.
The Takeaway
The manufacturing industry is necessarily one that involves significant risk to workers’ health and safety. On-the-job accidents and injuries are common, as are illnesses and injuries that may emerge across the long term. The good news, though, is that it is possible for manufacturers to prevent on-the-job injuries through strategies that promote a culture of safety on the worksite. This includes prioritising regular and comprehensive safety training. It also involves the mandated use of protective equipment and other safety gear. In addition, limiting workers’ exposure to hazardous materials and reducing the risk of overwork and fatigue are fundamental to promoting worker safety. Moreover, varying workers’ job roles can reduce the likelihood of repetitive motion injuries, one of the most common threats to employee safety in the manufacturing industry.