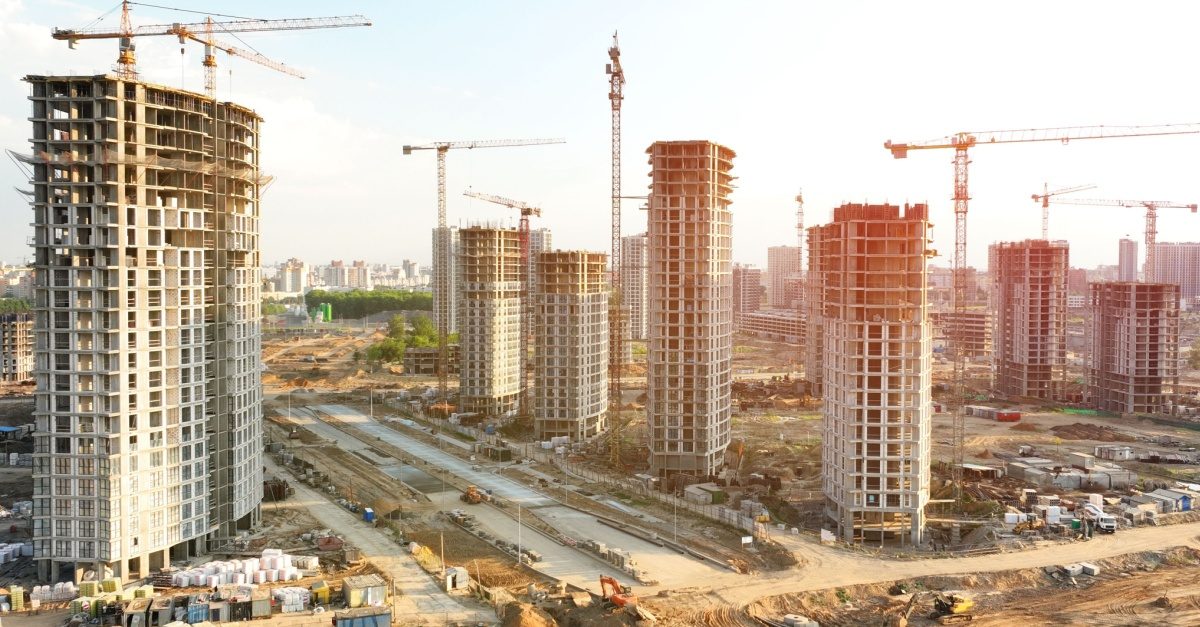
Best Practices for Quality Control in Construction Projects
Your ability to implement excellent quality control measures is key to building a structure that excels in safety, efficiency, and client satisfaction. To achieve this, you must create systematic processes that ensure precision and reliability at every phase. You should be able to catch problems before they become costly issues. Construction costs are increasing worldwide. Great Britain, for instance, noted a 4.2% rise in construction output value in 2023—reaching GBP£ 139,029 million—despite the 16% slowdown in new orders for public infrastructure and private housing. (1)
But construction quality management isn’t as simple as it sounds. It involves an intricate web of precision, teamwork, and meticulous attention to detail. This article provides insights into quality assurance and discusses how to optimise your cost and workflows while building the foundation for successful project delivery.
Establishing a Robust Quality Control Framework
Exceptional quality control lies in developing a comprehensive and adaptable framework. A holistic approach touches every aspect, from initial design conception to completion and handover. While you must create a quality control plan, it pays to be flexible and thorough across all stages of construction.
In doing so, you’re not just preventing mistakes; you’re also proactively safeguarding the entire project lifecycle as a construction quality control manager.
Strategic Planning and Preliminary Assessment
Invest significant time in strategic planning before breaking ground. You must conduct thorough feasibility studies, detailed risk assessments, and project scoping.
A construction quality management plan should include the following:
- Detailed project requirements analysis
- Identification of potential technical and logistical challenges
- Comprehensive stakeholder expectations mapping
- Initial quality benchmarking against industry standards
A well-designed quality management approach protects your project from structural weaknesses, compliance risks, and potential failures. Hence, it involves rigorous planning to identify potential pitfalls and minimise their impact.
Comprehensive Document Management and Tracking
Meticulous documentation is the cornerstone of effective quality control. Tracking every aspect of your project is a must. You can streamline this process by using inspection and test plans or ITP templates for construction. These standardised documents are tailored for every activity, including electrical, mechanical, civil, and instrumentation works. Every verification task guarantees consistency, creates clear accountability, and provides a transparent record of your project’s quality levels.
Technological Integration
Modern construction quality control transcends traditional clipboard inspections, which may be prone to unintended oversights and errors. Embrace digital technologies like Building Information Modelling (BIM), project monitoring software, real-time monitoring systems, and advanced data analytics. These tools offer unprecedented insights into your performance. Issues are detected and addressed in no time.
Because of this capability, the UK’s construction and design software market will likely reach USD$ 0.56 billion this year (GBP£ 0.44 billion). The sector’s value is projected to cumulatively grow to 2.71% between 2024 and 2029, reaching USD$ 0.64 billion (GBP£ 0.50 billion) by then. (2)
Workforce Training
Effective quality control strategies don’t just involve systematic testing, review, and validation; they also cover one of your most important resources—your workforce.
To ensure your workers’ competencies, consider the following aspects:
- Technical training: While waiting to hire more skilled trade workers, construction managers must focus on their current team’s expertise and maintain exceptional work standards. Invest in continuous training programmes that teach technical skills and impart quality consciousness to construction professionals.
- Developing a culture of quality: Creating an environment of quality occurs when every team member understands their role and is fully aware of the standards and regulations. Each individual must be responsible for maintaining high standards. You can also implement programs that reward positive behaviour.
Skilled labour shortages bug the construction industry worldwide. In the UK, for example, a report revealed that the construction industry has the highest number of vacancies, and 36% of these vacancies were related to skill shortages. (3)
Poor workmanship can lead to costly delays and corrective actions. Thus, apart from investing in new tools and reliable equipment, it’s critical to find the right workers who possess the skills and experience needed for your project.
Material Selection and Verification
The quality of your materials and work directly impacts your project’s long-term performance and customer satisfaction. It’s more critical to establish stringent procurement processes than merely looking at costs. Conduct exhaustive material testing, verify supplier credentials, and maintain detailed records of origins and performance histories. Make sure that your material transportation methods are reliable enough to withstand external and internal pressures.
Risk Management Strategies
Construction processes are complex ecosystems with multiple interconnected variables. Risks can emerge from numerous sources, including human factors, technological limitations, regulatory changes, environmental conditions, logistical issues, and job site-specific challenges.
You can that by developing comprehensive risk assessment protocols that identify the following:
- Potential vulnerabilities across design
- Material selection
- Workforce capabilities
- Environmental factors
Risk management in construction is an active and dynamic process of anticipation, assessment, and strategic intervention. Your ability to identify, evaluate, and mitigate potential risks can mean the difference between a smooth project and one that’s constantly facing costly issues.
Proactive Problem Solving
Advanced risk mitigation techniques provide more insights on how to enhance quality control in construction projects. You can take this essential construction activity further with these intuitive methods:
- Developing scenario-based training modules: Create modules that simulate real-world challenges your team might encounter. Training scenarios that replicate complex construction sites, unexpected material failures, or changing environmental circumstances can be a good start.
- Creating adaptive response protocols: Unlike rigid procedures, adaptive response protocols empower your construction crew to quickly and effectively respond to unexpected situations. Establish flexible guidelines that allow your staff to make intelligent decisions in real-time.
- Implementing predictive analytics: This tool transforms raw project data into actionable insights that can prevent potential issues before they arise. Modern construction firms use project management software and other advanced tools to gather historical data and current site information, weather patterns, material performance, and workforce productivity metrics to create predictive models. As such, you can adjust your approach before problems arise.
- Establishing cross-sectional communication channels: This breaks down traditional silos between different project teams and facilitates collaborative problem-solving. Create a unified platform for your design team, site managers, procurement specialists, and quality control experts. They should be able to share insights, flag potential issues, and collaborate on solutions when they need it most.
Your goal is to create an adaptive approach to project management that goes beyond compliance. Integrating these advanced methods transforms your quality assurance framework into an intelligent system that anticipates and prevents potential challenges.
Regular Inspections and Continuous Improvement
Quality management requires continuous evaluation and refinement. Schedule regular, comprehensive inspections at critical project milestones. Use these inspections not just for compliance checks but as opportunities for learning and improvement.
Begins with structured visual evaluations that leverage human expertise and technological tools like high-resolution imaging, drone surveillance, and sensors. These multi-dimensional assessments capture nuanced details that might escape traditional inspection methods. You can also incorporate advanced diagnostic techniques, data-driven insights, and collaborative feedback mechanisms.
Compliance and Regulatory Navigation
Authorities across different jurisdictions assign specified standards to guarantee the quality of construction processes and activities. These regulations are revised regularly to adapt to the changing times.
Staying ahead of evolving building codes and construction guidelines is non-negotiable. Regularly update your knowledge of local, national, and international construction standards. Develop compliance checklists that adapt to changing regulations and industry best practices.
Final Thoughts
Adopting comprehensive quality management strategies blends technical expertise, strategic thinking, and a genuine commitment to delivering exceptional results. Finding the best methods that work for you may require a steep learning curve. However, the time and money spent on these crucial activities yield invaluable benefits.
Apart from efficiency, you can ensure that every aspect of your project meets the highest standards of quality and safety. It also prevents costly rework, reduces potential legal challenges, protects your reputation, and saves significant resources. It’s the backbone of every successful construction project.
Citation
- ‘Construction statistics, Great Britain: 2023’. Source: https://www.ons.gov.uk/businessindustryandtrade/constructionindustry/articles/constructionstatistics/2023#:~:text=The%20value%20of,was%20public%20housing.
- ‘Construction and Design Software – United Kingdom’. Source: https://www.statista.com/outlook/tmo/software/productivity-software/construction-and-design-software/united-kingdom#:~:text=The%20United%20Kingdom%27s,0.64bn%20by%202029.
- ‘Coping with skill shortage within the UK construction industry: Scaling up training and development systems’. Source: https://www.sciencedirect.com/science/article/pii/S209044792300285X
Advance the capabilities of your business with IoSCM. Call 0800 1422 522 for more information.