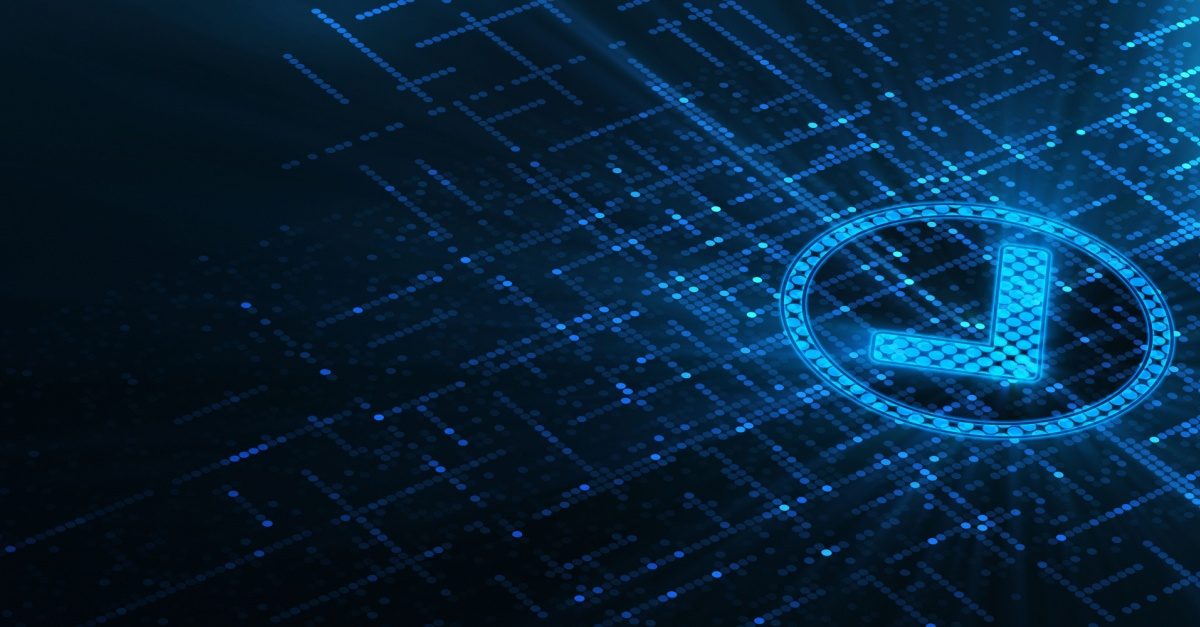
Ensuring Excellence: The Importance of Quality Control in Manufacturing
Quality control is a cornerstone of manufacturing that directly impacts product reliability, customer satisfaction, and operational efficiency. Maintaining robust quality control processes is beneficial and essential in an environment where customers demand high standards and regulations are increasingly stringent. This article examines the vital role of quality control in manufacturing, its key components, and the strategies businesses can adopt to foster a culture of excellence, ensuring their success.
Understanding Quality Control in Manufacturing
Quality control (QC) encompasses various practices and procedures to ensure products meet specific standards and requirements. This process begins during the initial stages of production and continues through to the final inspection before goods are shipped. The primary goal of quality control is to identify and rectify defects, ensuring that every item produced meets the desired specifications.
Effective quality control is critical for several reasons.
It enhances customer trust and mitigates the risk of costly recalls and rework. For instance, in the automotive sector, a single defect can lead to significant safety issues, prompting recalls that can cost millions in sectors such as manufacturing, where competition is fierce, and margins can be tight. Maintaining high-quality standards is vital for staying ahead. A thorough QC process can increase efficiency, reduce waste, and improve profitability.
Manufacturers often face challenges in establishing effective quality control systems. Common issues include insufficient training, lack of clear guidelines, and inadequate resource allocation. To overcome these obstacles, businesses must prioritise quality as a core value and integrate QC into their overall operational strategy. Doing so creates an environment where quality is everyone’s responsibility, from the production floor to upper management.
Quality Planning
The initial phase involves defining quality standards and objectives that align with customer expectations and regulatory requirements. Quality planning sets the foundation for all QC activities and helps ensure that all team members understand the quality goals. For example, a manufacturer might target reducing defects to less than 1% of total production, aligning internal standards with customer satisfaction metrics.
Inspection and Testing
Regular inspections and testing of raw materials, in-process components, and finished products are critical to identifying defects early in production. Techniques such as statistical sampling, visual inspections, and automated testing uphold quality standards effectively. For instance, in the production of rubber components, manufacturers might implement routine tensile strength tests to ensure the materials can withstand the intended use without failure.
Building Relationships with Trusted Suppliers
Collaborating with trusted suppliers ensures that the materials used in production meet rigorous quality specifications. Trusted rubber manufacturers, for example, play a critical role in providing high-quality components essential for durable and reliable products. Clear communication channels with suppliers help manufacturers set and enforce quality expectations. Regular audits and performance reviews strengthen these partnerships, fostering a sense of accountability and mutual commitment to quality,
Documentation and Reporting
Maintaining thorough documentation of quality control processes, inspection results, and corrective actions is essential for tracking performance over time. This transparency helps manufacturers identify patterns and areas for improvement, fostering a culture of continuous enhancement. Companies often use sophisticated quality management software to track quality metrics and compliance with industry standards.
Continuous Improvement
Quality control should not be viewed as a one-time effort but rather as an ongoing commitment to excellence. Manufacturers can adopt methodologies to drive continuous improvement, systematically reducing errors and enhancing product quality.
The Role of Technology in Quality Control
Technology is pivotal in enhancing quality control processes in modern manufacturing. Advanced technologies such as automation, artificial intelligence, and machine learning can significantly improve inspection accuracy, reduce human error, and increase efficiency.
Automation can streamline repetitive quality control tasks, allowing employees to focus on more complex issues that require human oversight. For instance, automated vision systems can quickly and accurately inspect products for defects at various manufacturing stages. These systems use cameras and sophisticated algorithms to detect product inconsistencies, thus identifying issues that might be missed during manual inspections.
“Data analytics can provide invaluable insights into quality trends”
Furthermore, data analytics can provide invaluable insights into quality trends, enabling manufacturers to make informed decisions based on real-time data. For example, if a manufacturer notices a spike in defects related to a particular machine, they can immediately investigate and rectify the issue before it escalates. By harnessing technology, businesses can enhance their quality control efforts, improving product consistency and customer satisfaction.
Implementing these technological solutions may require initial investment; however, the long-term benefits—including reduced defects, lower costs, and higher customer loyalty—typically outweigh the upfront expenses. As the manufacturing industry continues to evolve, embracing technology in quality control will be essential for maintaining a competitive edge.
Implementing Quality Control Strategies: Best Practices
To ensure excellence in manufacturing through quality control, companies should consider adopting several best practices. These include clearly defining quality objectives, embracing lean manufacturing principles, conducting regular audits, engaging employees, and monitoring customer feedback.
Establishing Clear Quality Objectives
Clearly defined quality goals serve as a roadmap for the entire organisation, aligning efforts across departments. These objectives should be specific, measurable, and achievable, providing a clear vision for quality expectations. Regularly reviewing and updating these objectives ensures they remain relevant and adaptable to changing market demands and regulatory standards.
Utilising Lean Manufacturing Techniques
Implementing lean principles helps identify and eliminate waste within the production process. By streamlining operations, manufacturers focus on producing high-quality products efficiently.
Conducting Regular Audits
Frequent audits of quality control processes help identify weaknesses and areas for improvement. These audits should involve internal and external assessments to provide a comprehensive overview of quality performance.
Engaging Employees in Quality Initiatives
Encouraging employees to take an active role in quality control leads to a greater sense of ownership and responsibility. Training and empowering staff to identify and report quality issues enhances performance.
Monitoring Customer Feedback
Actively seeking and analysing customer feedback provides valuable insights into product quality. Manufacturers should use this information to refine their processes and promptly address concerns.
Future Trends in Quality Control
Quality control in manufacturing is continuously evolving, with several emerging trends reshaping the industry, including the following:
Increased Integration of AI and Machine Learning
As artificial intelligence technologies advance, their integration into quality control processes is becoming more prevalent. Machine learning algorithms can analyse vast amounts of data to identify patterns, predict defects, and suggest improvements. This proactive approach helps manufacturers address quality issues before they occur, enhancing efficiency and customer satisfaction.
Sustainability and Quality
As environmental concerns grow, manufacturers are increasingly focusing on sustainable practices. Quality control plays a pivotal role in ensuring that sustainable materials and processes do not compromise product quality. For instance, new quality standards may need to be developed to address biodegradable materials or recycled content while maintaining performance expectations.
Remote Inspections and Quality Verification
The COVID-19 pandemic accelerated the adoption of remote working practices, including in quality control. Remote inspections using video conferencing tools and digital reporting enable manufacturers to maintain compliance and quality assurance without needing physical presence. This shift is leading to more flexible and efficient quality control operations.
In Conclusion
Quality control is the backbone of successful manufacturing. It ensures products meet the highest standards while fostering customer trust and loyalty. By embracing robust strategies and integrating innovation into their processes, manufacturers can achieve operational efficiency and long-term success. Staying ahead of industry trends and prioritising quality at every level will enable businesses to remain resilient and competitive in an ever-evolving marketplace.
The IoSCM Manufacturing and Production Academy offers manufacturing qualifications from Level 2 to Level 7. Not sure which course is for you? We promise to deliver outstanding support from the very first call—get in touch today.