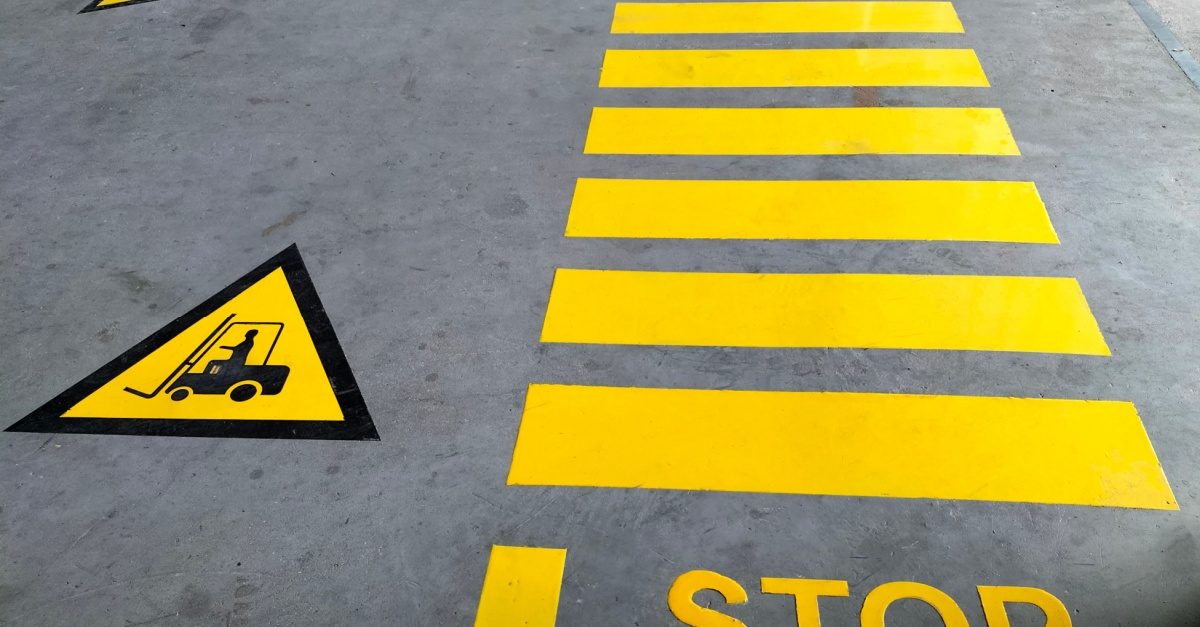
Common Warehouse Safety Risks and How to Address Them
When it comes to supply chain management, maintaining control, stability and safety across all facilities throughout the delivery life cycle is vital. Warehouses and similar facilities are inherently there to safely and efficiently pass goods and commodities through, facilitating the transportation of goods from manufacturers and suppliers to buyers and consumers. Management is responsible for the safety of warehouses, and overlooking certain aspects can spell disaster. Incidents—however innocuous on the surface—can halt operations, damage products, and, most importantly, put worker health and well-being at risk. As warehouses are the proverbial backbone of the logistics sector, they face numerous daily safety challenges that, if left unaddressed, can lead to accidents and financial repercussions. This article delves deeper into the common health and safety risks in warehouses, focusing on product damage, and provides actionable strategies for managing these effectively.
Are Warehouses a Risk to Employees?
The issue of warehouse safety isn’t exclusively confined to worker well-being – it encompasses a wide range of protocols and procedures designed to create a secure and optimised working environment.
Recent data suggests that the warehousing sector experiences higher rates of workplace injuries than many other industries. This illustrates the importance of implementing strict and robust safety measures to safeguard both workers and the products that are being transferred through the facility.
Common Safety Risks in Warehouses
1. Poor Material Handling
A prevalent risk in warehouses is improper material handling, which can cause potentially serious injuries for workers while also increasing the risk of product damage from falling or breaking. Poor lifting techniques, insufficient storage support, and misuse of handling equipment can all compound this safety risk.
2. Environmental Control
Some warehouses need to be fitted with stable temperature and humidity controls; otherwise, products (particularly perishables) can quickly degrade. Poor airflow and distribution can also contribute to this, which can be exacerbated by moisture damage. Warehouses need to ensure any airflow equipment like compressed air dryers are working properly and regularly tested.
3. Insufficient Staff Training
Proper training for warehouse staff is also vital, as lapses in knowledge, handling and awareness can cause safety incidents. Whether it’s training in safe equipment operation, signage, PPE, emergency evacuations, storage protocols, or anything else, overlooking safety knowledge is a recipe for disaster.
4. Poor Warehouse Layout
Disorganised and cluttered warehouses can create numerous hazards, from obstructed pathways and overloaded shelves to huge backlogs of orders and difficulties in accessing fire exits, among others.
5. Forklift Accidents
Forklifts and other warehouse machinery are essential, but they pose significant risks if not operated correctly and safely. Forklift accidents can cause severe injuries and excessive product damage if equipment is not handled in line with strict instructions. There is also the risk that trained personnel may lose their licences if found to be at fault.
6. Slip, Trip, and Fall Hazards
Uneven, wet, cluttered, and poorly lit surfaces and rooms can increase the risks of slips, trips, and falls for staff. Repeat accidents in this vein will put workers at increased risk while potentially damaging products in transit.
7. Inadequate Fire Safety Measures
Fire protection, prevention and response strategies are nothing to overlook and can often lead to catastrophic consequences in warehouses if left to materialise. Not only will staff be put in extreme danger, but facilities and products can also be completely ruined if fires are exacerbated and spread.
8. Chemical Hazards
Improper storage and handling of hazardous materials, chemicals, and corrosive solutions can pose serious risks to people and products in storage, particularly those made from combustible materials.
How to Address Warehouse Safety Risks
Training
The first step in addressing and mitigating safety risks in a warehouse is to implement strict, regular training for all staff, whether full-time or on a contractor basis. This training should cover all aspects of operations, including proper lifting techniques, safe machinery and equipment operation, hazardous material handling, and emergency response procedures. Regular refresher courses should be established to ensure all staff remain up-to-date with the latest safety protocols and recommendations.
Facility Design
Warehouse managers should design their facilities with safety in mind, ensuring clear and spacious aisles for easy movement of staff and equipment carrying large amounts of products. Proper signage, adequate lighting and floor markings will make this easier, as will reachable and reinforced bulk storage areas to offer stable stacking for product containers.
Well Maintained Equipment
Warehouse equipment should be regularly maintained, serviced, tested, and repaired to ensure it works properly all year round. Warehouse managers should enroll in preventative maintenance programmes, where external specialists visit and test equipment for faults and rectify them to ensure the risk of accidents and product damage is kept to a minimum.
Utilise Technology
The same can be extended to any new technology solutions which can aid and improve safety management in warehouses, such as Internet of Things (IoT) sensors and real-time asset tracking solutions powered by Bluetooth Low Energy (BLE) or Radio Frequency Identification (RFID) for monitoring product and staff movements in facilities.
Advanced Material Handling
Advanced material handling systems are worth considering to enhance safety in warehouses and reduce the risk of human error. Conveyor systems, robotic palletisers, and automated storage and retrieval systems (AS/RS) can all help reduce manual sorting, transferring, and stacking cases of products onto pallets, thereby reducing damage.
Enhanced Environmental Control
Maintaining optimal environmental conditions will help preserve product quality. Managers should consider installing enterprise-grade heating, ventilation and air conditioning (HVAC) systems, compressed air dryers, and temperature and humidity monitoring systems to ensure good air quality and airflow throughout the facility. Working in tandem with zonal and smart heating controls, these systems will give warehouse managers complete control over the conditions in each space of their facilities.
Establish a Safety Culture
Finally, warehouse safety should be instilled from the top down and firmly ingrained into a workplace culture. Managers should conduct regular safety audits and risk assessments to identify emerging and potential hazards before they lead to potentially harmful or risky incidents. Involving employees in the safety audit process will ensure their perspectives are included, with the findings and results influencing safety processes and procedures in the long run.
Next Steps to Enhance the Safety of Your Facility
Addressing warehouse safety risks is never a one-and-done process; it requires warehouse managers to make continuous changes, adjustments and investments in the right training, technology and processes to ensure the collective safety of their products and staff.
Implementing the above strategies will allow managers to create a safer and more secure facility. Still, it’s up to managers to ensure they’re not doing this purely as a compliance exercise. They must adapt and alter their strategies accordingly to account for emerging changes and fluctuations in their supply chains.
With such importance placed on the success of warehousing within a business, at the Institute of Supply Chain Management (IoSCM), we offer a range of professional qualifications, carefully designed to match modern business’ needs and upskill professionals at all stages of their warehousing careers. Call 0800 1422 522 to speak with a member of the team about how we can help you.